-
What is the Zone method?
Date posted:
-
-
Post Author
espadmin
1. What is the ZONE method?
The Hottel Zone method is one of the most widely used techniques for predicting radiation heat transfer in furnaces. In this method, the furnace chamber is subdivided into volume and surface zones. Each zone is assumed to have uniform temperature and radiative properties. Radiation exchange between the zones is then described by a set of simultaneous heat balance equations, which include terms for the incident and leaving fluxes at each surface zone. The leaving flux is the sum of the emitted and reflected components of radiation at a surface, and for a gas zone, it includes the emitted and scattered components.
These equations include terms called [GLOSS]directed flux areas[/GLOSS] (the units are in m2), which determine the radiant interchange between each zone pair. The directed flux areas are in turn derived from [GLOSS]direct exchange areas[/GLOSS] and[GLOSS]total exchange areas[/GLOSS]. The exchange areas describe the exchange of radiation between each pair of zones. These are rather like [GLOSS]view factors[/GLOSS] between surfaces except that they take account of the absorbing gas. Exchange areas need to be derived for every surface-surface, surface-volume, and volume-volume pair. They are a function of the following factors:
q The relative geometric orientation of the zone pair and presence of any third surface that might obstruct the view.
q The emission and attenuation of radiation by absorbing gases such as combustion products in the radiating volume.
q Total exchange areas also take account of radiation exchange between a zone pair that occurs via reflection from all other surfaces in the furnace.
An important feature of the Zone method is that direct and total exchange areas are defined such that they are independent of temperature, provided gas composition remains constant. They can therefore be calculated once for a given furnace enclosure geometry and for a given set of radiative properties ([GLOSS]emissivity[/GLOSS], gas [GLOSS]absorption coefficient[/GLOSS]). If changes are simulated that do not affect these properties (e.g. changes in fuel firing rate, thermal load or temperature) then it is not necessary to recalculate exchange areas every time. Also exchange areas do not need to be updated during iterative solution of the radiation balance equations.
2. Allowance for non-grey gases
The Zone method was mainly developed because of its ability to handle non-grey gases.[GLOSS]Non-grey gas[/GLOSS]behaviour can be conveniently handled in the Zone method by using the [GLOSS]mixed grey gas model[/GLOSS] or [GLOSS]weighted sum of grey gases[/GLOSS] model (see CF44) in which the combustion gases are represented by a mixture of grey gases plus a clear gas. Radiation exchange factors and heat fluxes between zones are calculated for each grey (plus the clear) gas component within this model. This approach works well for homogeneous radiating gases. The method is less adaptable to situations where gaseous composition varies between zones and where absorption coefficient is a function of position.
3. Single zone model
At its simplest level, a furnace can be represented by a single volume (gas) zone, which is surrounded by one or two surface zones representing for example the load or heat sink surfaces and the insulating walls. This is often referred to as a zero-dimensional or [GLOSS]well-stirred zone model[/GLOSS] (similar to the well-stirred reactor model in chemical engineering). This model can provide reliable prediction of radiation in box shaped furnaces and batch processes where the load surface temperature is relatively uniform throughout the heating cycle. It is also applicable where the load temperature is sufficiently low compared to the walls and flame, that variation in its temperature does not significantly affect the net radiant flux to the load (e.g. tube surfaces in a boiler or fired vaporiser).
4. Long furnace model
If the furnace length is long compared to its cross section or diameter, then it is often reasonable to assume that temperature variation in the furnace is dominant along the length, and temperatures and properties can be assumed to be uniform at any cross section. In this case, one can employ the so-called 1-D or ‘[GLOSS]long-furnace model[/GLOSS]’ where the radiating enclosure is divided into a longitudinal series of well-stirred zones (Fig.1). Combustion gases flow between the zones. Radiation exchange between zones also occurs.
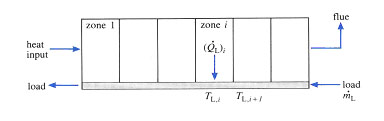
Fig.1 A long furnace Zone model of a continuous furnace.
In the simplest type of long furnace model, inter-zone radiation exchange is ignored. In more accurate long-furnace models, full account is taken of the longitudinal radiation exchange between all surfaces and gases in the furnace enclosure. This demands calculation of all radiation exchange factors between every zone pair. If there are 10 volume and 20 surface zones for example, a total of 30×30 exchange factors have to be defined.
The long furnace model is very well suited to applications such as tunnel kilns and continuous steel reheating furnaces, where the load transport through the furnace imposes a significant length-wise temperature variation.
5. Multi-dimensional Zone models
The zone method can be applied to more complex geometries using 2-D and 3-D arrangements of zones. Both cylindrical (Fig.2) and rectangular zoning has been applied. These models are capable to allowing for and predicting longitudinal and cross sectional temperature and property variations. They are applied to large furnaces where the assumption of well-stirred behaviour cannot be made; for example, in furnaces in which the flame occupies a significant proportion of the radiating volume. Large numbers of exchange factors have to be defined in these models, so their geometric specification can be quite complex and time consuming. Examples where 2-D and 3-D zone models might be applied are process heaters and reformers, glass melting tanks, and the combustion chambers of water tube boilers.

Fig.2 A 2-D axi-symmetric model of the radiant section of a fired process heater.
Sources
1. Hottel H.C. and Sarofim A.F., Radiative Transfer, McGraw-Hill, 1967.
2. Noble J.J., ‘The Zone Method: Explicit Matrix Relations for Total Exchange Areas’, Int.J.Heat Mass Transfer, vol. 18, pp. 261-269, 1975.
3. Rhine J.M. & Tucker R.J., Modelling of gas-fired furnaces and boilers, McGraw-Hill, 1990.