-
What is the zinc roasting process?
Date posted:
-
-
Post Author
dev@edge.studio
1. Zinc roasting process
Zinc roasting chemistry
The zinc roasting process is a process stage where in the presence of oxygen and high temperature (about 920-950ºC) zinc sulphide concentrates react to zinc oxide. The zinc sulphide (ZnS, sphalerite) concentrates include also various amounts of other metal sulphides. For example iron appears not only in the forms of FeS and FeS2 but also in the zinc sulphide lattice. Because of the variable content of impurities and particle sizes in zinc concentrates from different mines, the zinc plants usually mix the concentrates of different quality to stabilise the roasting. The concentrate mix is converted to oxides according to reactions
Because of the iron in the zinc sulphide lattice, some zinc ferrite (ZnO.Fe2O3) is also produced during roasting. This zinc ferrite along with the other resulting solid oxides (common name [GLOSS]zinc calcine[/GLOSS]) are treated with weak sulphuric acid in the next process stage called [GLOSS]zinc roasting leaching[/GLOSS], where ZnO dissolves. The remaining zinc ferrite is treated in following process stages in reactors with high sulphuric acid content in order to dissolve the ferrites. The iron is then precipitated from the solution.
As can be seen from the reaction enthalpies, the roasting process is exothermic. The released energy is usually used in the production of electricity, district heat and low pressure steam by cooling the [GLOSS]zinc roaster furnace[/GLOSS] and the [GLOSS]waste heat boiler[/GLOSS] with tubes of circulating water.
The roasting reaction also produces sulphur dioxide rich waste gas, which can be used in different process stages making by-products like sulphuric acid and liquid mercury.
Zinc roaster furnace
The most common way of zinc roasting is to burn the zinc concentrates in a [GLOSS]fluidised bed[/GLOSS] of a zinc roaster furnace. After a cold shut down the start-up of the zinc roaster furnace starts with feeding in ready-made calcine and air to form a floating calcine bed. The bed is heated with start-up burners up to about 450ºC and with coal up to 850°C. At that temperature the zinc concentrate mix ignites and the continuous concentrate feed to the furnace can begin. During the roasting process the fine concentrate particles agglomerate into bigger calcine particles. The agglomeration can be affected by damping the concentrate feed with water before it is fed to the furnace. The water functions as a binding agent affecting the concentrate particle size and intensifying the burning process.
An example of a fluidised bed zinc roaster furnace is to be found at the Boliden Kokkola Oy zinc plant in Finland, where there are two furnaces in use. In Kokkola’s zinc roaster furnace the main input variables are concentrate feed, airflow, water feed to the concentrate mix and the bed and oxygen feed to the airflow. Some of these input variables are used to control the stability of the burning process. For example, in Kokkola the concentrate feed and concentrate water feed are used to control the temperatures in the bed and in the waste gas before the waste heat boiler. The bed temperature can also be decreased by injecting furnace water in to the bed where it evaporates and cools down the bed. Other important output variables are the furnaces windbox pressure and the oxygen content in the waste gas. In Kokkola the oxygen coefficient of burning is used only for monitoring of the roasting process. A schematic picture of the zinc roaster in Boliden Kokkola Oy is shown in Figure 1.
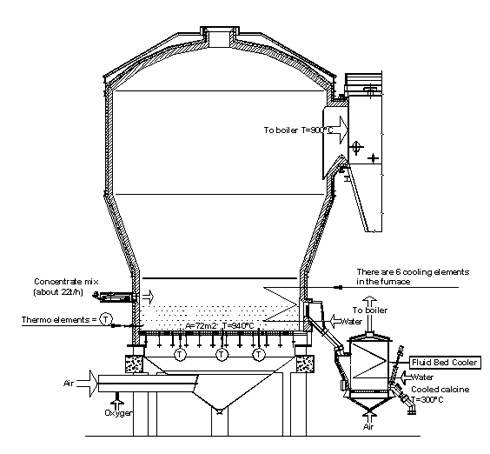
Fig 1: A schematic picture of a zinc roaster furnace and fluid bed cooler in Boliden Kokkola Oy
Depending on the amount of impurities in the zinc concentrates the roasting process can be replaced by acid pressure leaching (iron content over 5%) or sintering roasting techniques (high lead content).
Acknowledgements
Special acknowledgement to the Boliden Kokkola Oy and Outokumpu Research Oy for the help and information.
Sources
[1] H. Takala, Leaching of Zinc Concentrates at Outokumpu Kokkola Plant, Erzmetall, 1999.
[2] M. Metsärinta, P. Taskinen, S. Jyrkönen, J. Nyberg and A. Rytioja, Roasting Mechanisms of Impure Zinc Concentrates in Fluidised Beds, Yazawa
International Symposium at TMS 2003 Annual Meeting & Exhibition, edited by
F Kongoli et al., TMS, Volume I, ISBN: 0-87339-546-8, San Diego, pp.
633-646.
[3] M. H. Tikkanen, Helppoa termodynamiikkaa prosessimetallurgeille ja
kemisteille , 525, Otatieto *Oy,Kyriiri Oy Helsinki 1990
[4] F. Ajersch, Roasting of zinc feeds. Lead Zinc Short course,
Oct.21-22.2000, The Lead-Zinc 2000 Symposium, Pittsburgh, PA
[5] J. Valo, Simulation and Production Optimization of a Zinc Roaster Furnace, Master’s Thesis, University of Oulu, 2004.