-
What are the titanium dioxide and synthetic rutile manufacturing processes?
Date posted:
-
-
Post Author
dev@edge.studio
1. Introduction
The complete range of processes undertaken in the minerals processing industry was outlined in CF 255. This combustion file gives more specific detail of the processes in use for the manufacture of titanium dioxide and synthetic rutile.
2. Titanium Dioxide and Synthetic Rutile
Titanium dioxide, used principally as a pigment, is made by one of two routes: the sulphate or chloride processes. There is an economic and environmental preference for the chloride route, but at the present time the two technologies have approximately equal shares of the market. See Figures 1 and 2.
The raw material is also of significance in the choice of process, as rutile (92%-96% TiO2 ore) is insoluble in sulphuric acid, and is not suitable for the sulphate process, whereas ilmenite (45%-70% TiO2 ore) and some [GLOSS]slag[/GLOSS]s are not suitable for the chloride process. The availability of natural rutile is limited, and restricted principally to Australia (560.000 t.p.a. in 1993). Ilmenite can however be ‘[GLOSS]beneficiate[/GLOSS]d‘ to produce synthetic rutile by a high temperature [GLOSS]redox[/GLOSS] reaction with [GLOSS]coal[/GLOSS] in a [GLOSS]rotary kiln[/GLOSS] to separate the FeO. 630.000 t.p.a. of synthetic rutile was produced in 1993 from three plants in Australia, two in India, and one in each of Malaysia, Japan and USA.
In the sulphate process, the purified titanium oxide is separated as a hydroxide, TiO(OH)2, which is then dried, and heated in a rotary kiln through an [GLOSS]amorphous[/GLOSS] phase to give pure rutile,TiO2. In the chloride process, the purification process is carried out in a fluid bed. Thus, whichever route is used to produce TiO2 pigment, rotary kiln technology is required.
Synthetic Rutile is made by mixing the ilmenite ore with coal and heating under reducing conditions to ~1200oC in a rotary kiln to reduce the iron oxide to elemental iron. The flue gases are burnt in an incinerator immediately after the kiln. The kiln used in the sulphate process is unusual, in that it has a stationary cylindrical combustion chamber at the hot end of the rotary kiln, thus only hot [GLOSS]flue gases[/GLOSS] enter the kiln, and there is no direct flame heat transfer to the bed. This is because of the ‘sensitivity’ of the produce colour to excess heat, so the bed temperature is controlled very closely at ~950oC.
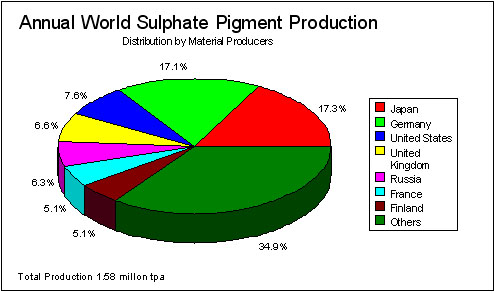
Figure 1 World TiO2 Pigment Production (Sulphate Route) for 1993 (Industrial Minerals Handy Book)
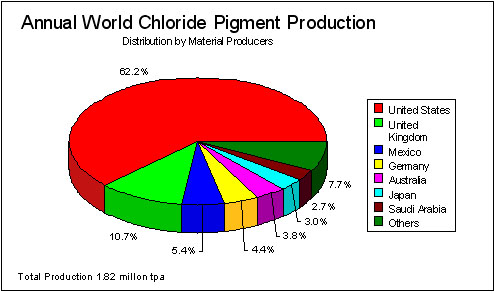
Figure 2 World TiO2 Pigment Production (Chloride Route) for 1993 (Industrial Minerals Handy Book)
Sources
[1] European Minerals Yearbook
[2] Industrial Minerals Handy Book