-
What are biomass fuel pellets?
Date posted:
-
-
Post Author
dev@edge.studio
1. Background
Biomass [GLOSS]fuel pellets[/GLOSS], in power generation industry, are produced in pellet mills. Pellet mills receive, sort, grind, dry, compress, and bag into a conveniently handled fuel, see Figure 1. The most common pellets are made from sawdust and ground wood chips, which are waste materials from trees used to make furniture, lumber, and other products. Resins and binders (lignin) occurring naturally in the sawdust hold wood pellets together, so they usually contain no additives. Nutshells and other materials are pelletised in some areas, and unprocessed shelled corn and fruit pits can be burned in a few pellet-stove designs [1].
Figure 1: Pellets
2. Production of Pellets
The most common raw materials for producing fuel pellets are the wood shavings and sawdust. However, other raw materials, such as bark, wood chips, agricultural stalk crops, sorted household waste, paper and wood waste are also utilised.
The pelletising procedure contains at least four steps [3]:
- Drying: the raw material cannot be palletised with a moisture content higher than 17%; the existing driers are the drum drier, steam drier and hot drier.
- Milling: the raw material is milled, normally by a hammer mill, to be uniform for feeding to the pellet mill.
- Pelletising: the loose material is fed into the palletising cavity; die rotation and roller pressure force the material through die, compressing it into pellets. Adjustable knives cut the pellets to the desired length. Pellet mills can be of the flat-die or vertical mounted ring die type. In the former case, the die is mounted flat and remains stationary while the powered rollers rotate. With the ring die, it is the die that rotates. As with the hammer mill, a certain amount of additional moisture is extracted with the pellet mill.
- Cooling: when the pellet leaves the pellet mill it is very hot, approx. 90-95oC. The palletising process releases moisture, which has to be removed along with the heat. The cooling process helps to stabilise, harden and form the pellets.
Another two steps maybe used as:
- Fines separation: residual fines are separated and returned to the process.
- Bagging/storing: the pellets are bagged automatically or stored in silo.
The main criteria for achieving high-quality pellets are:
- homogenous raw material,
- well conditioned raw material,
- right die specification.
The most important parameters of the raw material are the degree of [GLOSS]comminution[/GLOSS] and the water content.
3. Quality Aspects and Standards
The chemical constituents and moisture content of different biomass raw materials vary; therefore common characteristics of pellets are hard to define. The European and US quality standards for fuel pellets are shown in the Table 1. At the moment, there is no European standard for biomass fuels.
4. What Advantages do Fuel Pellets Offer?
The first appeal of pellets is their convenience: good logistic characteristics that make hygienic, safe and efficient transportation, storage and handling of the solid fuel both technically and economically feasible.
The small size of pellets allows for precisely regulated fuel feed. In turn, combustion air can be regulated easily for optimum burn efficiency since the amount of fuel in the burn pot is predictable and consistent. High combustion efficiency is also due to the uniformly low moisture content of pellets (consistently below 10% compared to 20 to 60% moisture content in cordwood). Uniformly low moisture, controlled fuel batches, and precisely regulated combustion air means high heat output and a relatively low level of CO emissions. As a biomass fuel, pellets offer the advantages of sustainable energy supplies through renewable raw materials. Using pellets also helps to reduce the costs and problems of waste disposal.
Pelletisation offers also a good possibility to transform waste materials, e.g. mixed plastics fractions (MPF) and plastics/paper fractions (PPF) separated from household waste, into such a form, which meets the fuel-feeding, mixing, grinding, etc. requirements of co-combustion, e.g. in pulverised combustion. Figure 2 demonstrates the production of fuel pellets from PPF and MDF.
Table 1: Pellet standards of different countries. [3]
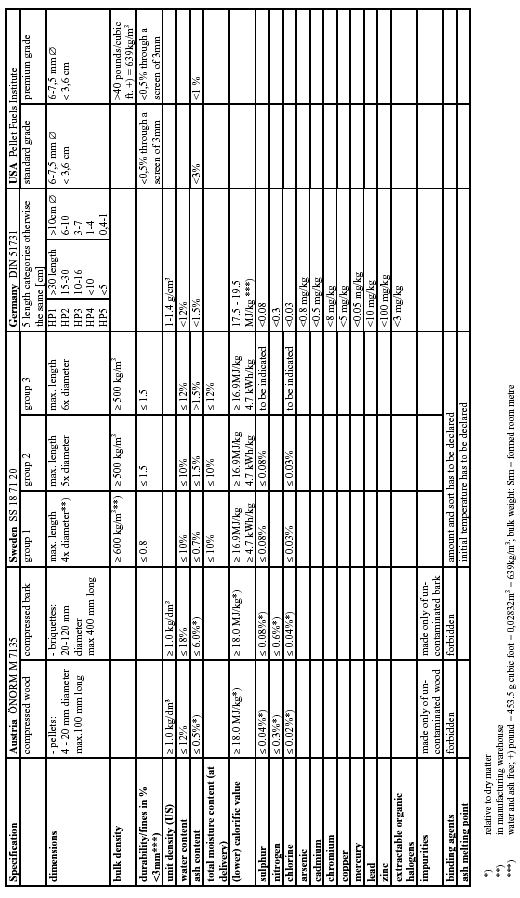
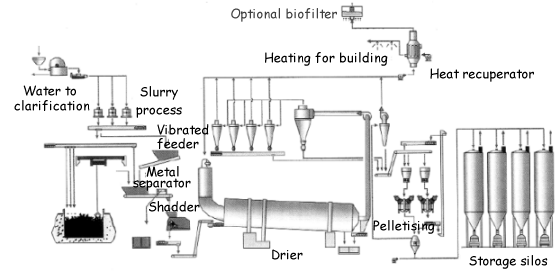
Figure 2: Process for production of fuel pellets from PPF and MPF. [2]
5. Where are Biomass Fuel Pellets Used?
Biomass fuel pellets, as substitute solid fuels in power generation, can be utilised in various combustion units:
- in fluidised bed combustor by added to the main fuel flow or via a separate feeding system; grinding of the pellets might be installed to provide more homogenous fuel mixture,
- in co-combustion in pulverised coal combustor mixed together with the main fuel and then grinded, or grinded separately and then mixed,
- in the common grate boilers,
- in small boilers and stoves.
Although this Combustion Files focuses on the industrial application of fuel pellets, it must be mentioned that the household utilisation of fuel pellets has a great and increasing importance.
Keywords:
Biomass, fuel, fuel pellets, fuel production, pellets, waste.
Source:
[1] Pellet Fuel Institute http://pelletheat.org/fuel/fuel.html
[2] L.A.A. Schöen & J. van Tubergen: Mechanical separation of mixed plastics from household waste and energy recovery in a pulverized coal-fired power station. A technical paper of the Association of Plastic Manufacturers in Europe. http://www.apme.org/literature/pdf/8035.pdf
[3] Asplan Vlak, AEBIOM, FastBranslePannor, Lambelet Heizungssyteme, Technische Universitat Munchen, Umdasch AG, Whitfield GmbH, UMBERA (2000): Woodpellets in Europe. Thermie B DIS/2043/98-AT project.
http://www.eva.wsr.ac.at/(en)/publ/pdf/pellets_net_en.pdf