-
How does black liquor burn?
Date posted:
-
-
Post Author
dev@edge.studio
1. Stages of Black Liquor Combustion
As a [GLOSS]char[/GLOSS] forming liquid with both high water (15-35 wt%) and [GLOSS]ash[/GLOSS] content (30-50 wt% of BLS) [GLOSS]black liquor[/GLOSS] (CF199) is a [GLOSS]biofuel[/GLOSS] with unique burning properties. As a char forming liquid, black liquor goes through four stages during combustion: drying; [GLOSS]devolatilisation[/GLOSS]/[GLOSS]pyrolysis[/GLOSS]; char burning; and [GLOSS]black liquor smelt[/GLOSS] [GLOSS]coalescence[/GLOSS] (Figure 1). The terms devolatilisation and pyrolysis are used interchangeably to describe the release of volatile organic matter. Devolatilisation is defined as this process occurring in an oxidizing or a reducing atmosphere while pyrolysis refers to it occurring in an oxygen free atmosphere. A unique feature of black liquor when compared to other biofuels is the dramatic swelling that can occur during the burning process.
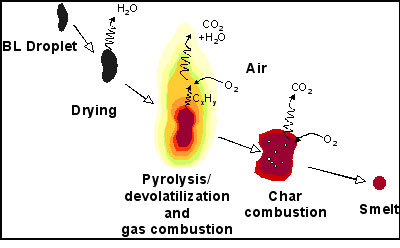
Figure 1. Stages of Black Liquor Combustion
Drying
The black liquor is sprayed into the recovery boiler (CF202) at a temperature close to its boiling point, absorbing heat from its surroundings by convection and radiation and begins to release water vapour. The rate of water release is determined by heat transfer limitations and in a recovery boiler the drying and devolatilisation stages overlap to a large extent.
Devolatilisation
Devolatilisation is the thermal decomposition of the organic compounds in black liquor and the subsequent volatilization of tars and lighter [GLOSS]hydrocarbons[/GLOSS] that then react with oxygen, CO2 and H2O in the gas phase. This process begins when the droplet reaches the temperature of about 200°C and continues until the particles are well over 450°C due to the rapid heating rates of the droplets in the recovery boiler. Under typical recovery boiler conditions, up to 50 % of the black liquor solids can be released during this stage.
An important feature of this stage is the swelling of the black liquor droplet. As water vapour and volatiles escape, these gases cause the droplet to swell due to the elastic nature of the organic material. Volumetric expansions of 20 to 50 times the original volume are typical for [GLOSS]kraft process[/GLOSS] black liquors. The swelling leads to both a reduction in mass transfer limitations and a decrease in the rate of internal heat transfer. Sulphite liquors swell to a much lesser extent than kraft black liquors. This is due to the difference in the form of the organics after cooking though the specific compositions that lead to a high degree of swelling are not known.
Char Carbon Conversion
When the gases have been released there still remains a carbon matrix (char) and the majority of the ash. This carbon matrix can be oxidized by the gases: O2, CO2 and H2O. The sodium salts have a catalytic effect on the oxidation of the carbon matrix and black liquor chars react more quickly with oxidants than the chars of other carbon fuels. The rate of char burning is limited by mass transfer, rather than the reaction kinetics at the high temperatures in the recovery boiler. Swelling reduces these mass transfer limitations by opening up the internal pore structure.
The char carbon can also be oxidized through reactions with the inorganic components sodium sulphate, Na2SO4, and sodium carbonate, Na2CO3. The reduction of Na2SO4 to sodium sulphide, Na2S, is an important feature of the recovery boiler process and Na2SO4 can supply about 10% of the oxygen needed for oxidation of the char. The reaction of char with Na2CO3 is less important for the char oxidation, though it can lead to significant alkali fuming due to Na2CO3 decomposition at the highest temperatures.
Smelt Coalescence
As the char burns out, the remaining sodium salts are molten at typical recovery boiler temperatures and a single smelt bead is formed. For other fuels the sodium salts would be called ash but are in the case of black liquor a product to be recovered (CF199).
2. Sulphur and Sodium Release
Some sulphur is released during the devolatilisation stage with the volatilized hydrocarbons, while the majority is retained in the droplet as Na2S. The reduced sulphur compounds such as H2S, mercaptans, dimethyl sulphide and other organosulfur compounds are primarily released in the temperature range of 300-400 °C. These reduced sulphur compounds will readily oxidize above the tertiary air level provided there is good mixing.
Unlike sulphur, very little sodium is released during devolatilisation, while significant amounts (up to 10% of the total sodium) can be released during the char burning phase, primarily due to the reaction of the char with Na2CO3. These reactions are kinetically controlled and higher particle temperatures can therefore lead to higher sodium release (fuming). The primary sodium compounds released are NaOH and metallic sodium.
The volatilised sodium compounds can react with SO2 in the upper furnace to form Na2SO4. Higher temperatures in the lower furnace result in less sulphur being released but more [GLOSS]black liquor fume[/GLOSS]. Thus higher temperatures in the lower furnace can then lead to lower SO2 emissions.
Sources
T. N. Adams (Ed.), Kraft Recovery Boilers, Tappi Press, 1997.