-
What is the effect of roughness on surface emissivities of refractories?
Date posted:
-
-
-
Post Author
Neil Fricker
-
1. Background
[GLOSS]Surface emissivity[/GLOSS] is an important factor in determining radiant heat transfer within furnaces, boilers and other items of heating plant. The background to the concept of surface emissivity and data for the emissivity of ceramics and refractories is given in linked Combustion Files (CF 146, 148, 223).
This Combustion File considers the effect of surface roughness on the emissivity of refractories. The effect of surface oxidation on the emissivity of metals is addressed in CF 147.
2. Idealised description of surface roughness
The surface roughness (r’) is appropriately expressed as the ratio of the root mean square depth of the surface cavities (d) to the wavelength of radiation (l)
r’ = d/l. (1)
Surface roughness can be placed in two categories according to this criterion, bearing in mind that at very small values of r’ the surface will be a smooth [GLOSS]specular reflector[/GLOSS]:
· With relatively small cavities, the specular reflecting material is converted to a partially diffuse, partially specular reflector.
· Multiple reflections occur with surfaces possessing relatively deep cavities and the effective emissivity is significantly larger than that of a smooth surface.
The first category has been treated by Bennet and Porteus1, among others; a simple approach to the second category is given by examining a single cavity as shown in Fig. 1. An imaginary plane of area A2 is stretched across a cavity of area A1.
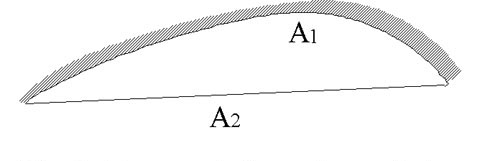
where r1 and e1 refer to reflectivity and emissivity of the smooth material. For a groove of angle 60°, for example, the emissivity increases by varying amounts, depending on the original emissivity, as shown in Table 1. Consequently, the apparent emissivity of a diffuse furnace wall can be enhanced by cutting grooves in the surface.
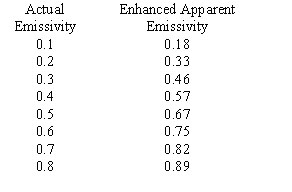
Table 1: The effect of surface roughness on enhancing emissivity
(Groove Angle 60°).
3. Radiative properties of real materials
Certain materials are inherently rough, those which are granular or fibrous, for example. The radiative properties of granular metal oxide refractories and fibrous materials are determined not by the surface layer but by scattering and adsorption by particles below the surface. The calculation of values of emissivity has been attempted but it is not easy to predict values accurately for real materials. The effect of grain size and material has been indicated by some practical measurements at 1200°C as shown in Table 2.
Oxide |
Grain size (mm) |
Emissivity |
Al2O3 |
2 – 25 |
0.35 |
|
15 – 80 |
0.43 |
|
90 – 120 |
0.53 |
MgO |
1 – 3 |
0.30 |
|
30 – 75 |
0.39 |
|
90 – 120 |
0.48 |
Cr2O3 |
0.5 – 1.5 |
0.72 |
|
1.5 – 8 |
0.95 |
Table 2: Effect of Grain Size on the Emissivity of Selected Oxides at 1200ºC
A typical granular refractory brick with a grain size of 60 mm would have grooves in the surface with an angle of approximately 60° and an enhancement of emissivity as given by the values in Table 1. A ceramic fibre board would also contain grooves of about 60°. Some stack-bonded boards would have a greater increase than shown in Table 1.
Rough surfaces should lead to higher emissivities for a particular material. This is particularly true for metals3 and there is some evidence, from Fig.2, that it is true when comparing certain refractory materials.
It is difficult to isolate this effect from differences in composition between these materials, even when these are small since minor variations in the amounts of certain compounds can affect emissivity as shown, for example by the data in CF 148 and 223. However, for the same material composition it has proved difficult to measure the effects of varying surface emissivity since, by nature, refractory materials are diffuse emitters and reflectors 4. The influence of surface roughness is not great compared to metals where the differences in surface behaviour between polished and oxidised surfaces is significant. (CF147)
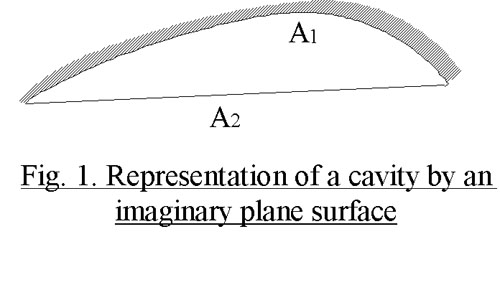
Fig. 2: Normal total emittance of refractory materials based on aluminium and silicon oxides:
Acknowledgements
This work was funded in part by the UK Heat Transfer and Fluid Flow Service (HTFS) and part supported by the UK EPSRC. The information contained within this file was first published in the Journal of the Institute of Energy. 74, No 500 September 2001 (pp 91 – 99). The permission of the UK Institute of Energy to reproduce it here is gratefully acknowledged.
Sources
[1] BENNET, H.E. and PORTEUS, J.D. J.Opt. Soc. Am., 1961, 51,123.
[2] GRAY, W.A. and MÜLLER, R. Engineering calculations in radiant heat transfer, Pergamon, 1974.
[3] DE WITT, D.P. and BERNICZ, R.S. Temperature, It’s measurement and control in science and industry, 4, 1 (Reinhold Publishing), 1972
[4] HAMPARTSOUMIAN, E. Spectral emittance measurements of furnace wall materials and coatings. Ceramics in Energy Applications Conference, Sheffield, IOP Publishing Ltd., 1990, 149-157.
[5] HAMPARTSOUMIAN, E, Hainsworth D, Taylor JM and Williams A. The radiant emissivity of some materials at high temperature. Journal of the Institute of Energy. 74, No 500 September 2001 (pp 91 – 99).