-
What is the effect of O2/RFG on coal dust explosion characteristics?
Date posted:
-
-
Post Author
espadmin
1. Introduction to oxy-coal combustion
Definition
In oxy-combustion of coal, the pulverised coal is burned in oxygen-enriched recycled flue gas at concentrations greater than 21% O2 (the concentration of oxygen in air). This may well provide advantages in carbon sequestration against other technologies such as pre- and post-combustion capture. However, the risk of dust explosions (CF310) increases significantly with increasing oxygen concentration and temperature. It is known that increasing the oxygen concentration will make the dust cloud more sensitive to ignition compared to a dust cloud in an atmosphere of pure air. In the literature some experimental data can be found on dust explosion characteristics for oxygen poor mixtures, which are important for inert conditions [1]. However, only very scarce data can be found on dust explosion characteristics in oxygen enriched mixtures. One objective of the European FP7 project RELCOM (Reliable and Efficient Combustion of Oxygen/Coal/Recycled Flue Gas Mixtures) was to research the influence of enriched oxygen concentrations on the dust explosion characteristics of three different coal types: Indonesian Sebuku coal dust, Pittsburgh coal n°8 and South African coal dust.
2. Dust explosion characteristics at increased oxygen concentrations
It can be expected intuitively that both the ignition sensitivity and the explosion violence increase with increasing oxygen concentration. In oxy-fuel combustion the inert component nitrogen is replaced by carbon dioxide from the recycled flue gas. Since carbon dioxide has a higher specific heat capacity than nitrogen it can be expected that the carbon dioxide will decrease the ignition sensitivity and explosion violence.
Ignition sensitivity: minimum ignition energy
The most important explosion characteristic for assessing the explosion sensitivity or ignitability is the [GLOSS]minimum ignition energy[/GLOSS] ([GLOSS]MIE[/GLOSS]). Indonesian Sebuku coal was out of the three tested coals the most sensitive for ignition in air and oxy-fuel atmospheres. The MIE of Sebuku coal in air lies between 30 mJ and 100 mJ, with a statistical estimate of 60 mJ. In O2/CO2 mixtures with oxygen concentrations from 20% up to 50% the MIE of Sebuku coal decreases from 82 mJ to 3.5 mJ and to 1.4 mJ in a 28 vol.%, 38 vol.% and 48 vol.% O2 in CO2 mixture respectively. This implies that the minimum ignition energy is significantly dependent on the oxygen concentration. For an oxygen concentration equal to 28% in CO2 more or less the same ignition risk is observed as in air. For higher oxygen concentrations Sebuku coal becomes very (MIE < 10 mJ) or extremely (MIE < 3 mJ) sensitive to ignition. Pittsburgh and South African coal on the other hand are almost insensitive for [GLOSS]electrostatic ignition[/GLOSS] in air but become very sensitive for ignition in a 50 vol.% O2 in CO2 mixture.
Because both the minimum cloud and layer ignition temperatures ([GLOSS]MCIT[/GLOSS] and [GLOSS]MLIT[/GLOSS]) decrease with increasing oxygen concentration the probability of ignition due to mechanically generated sparks increases significantly in oxy-fuel combustion [1].
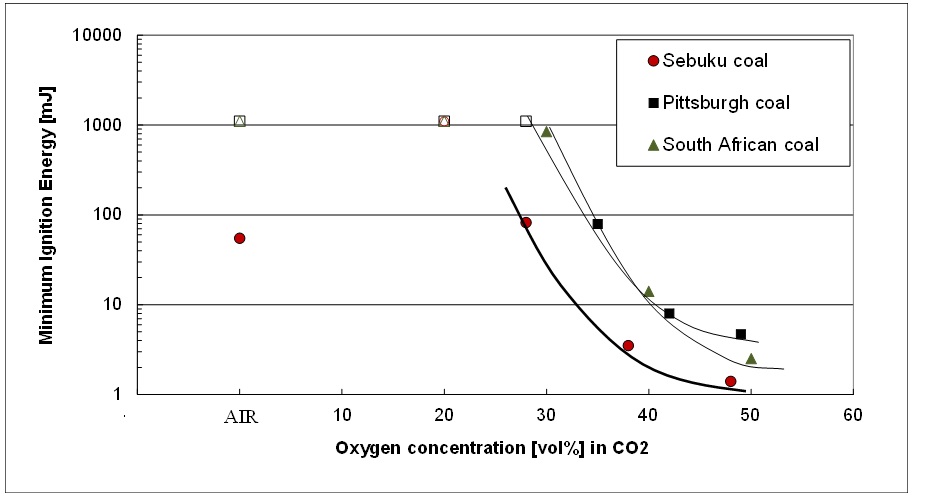
Figure 1: Influence of the oxygen concentration on the minimum ignition energy of coal
Explosion violence: maximum explosion pressure and maximum rate of pressure rise
The influence of increased oxygen concentration on the explosion severity characteristics, namely the maximum explosion pressure (Pmax) and maximum rate of pressure rise or [GLOSS]dust explosion constant[/GLOSS] ([GLOSS]Kst-value[/GLOSS]) was determined experimentally and the results are presented in Figure 2 and Figure 3.
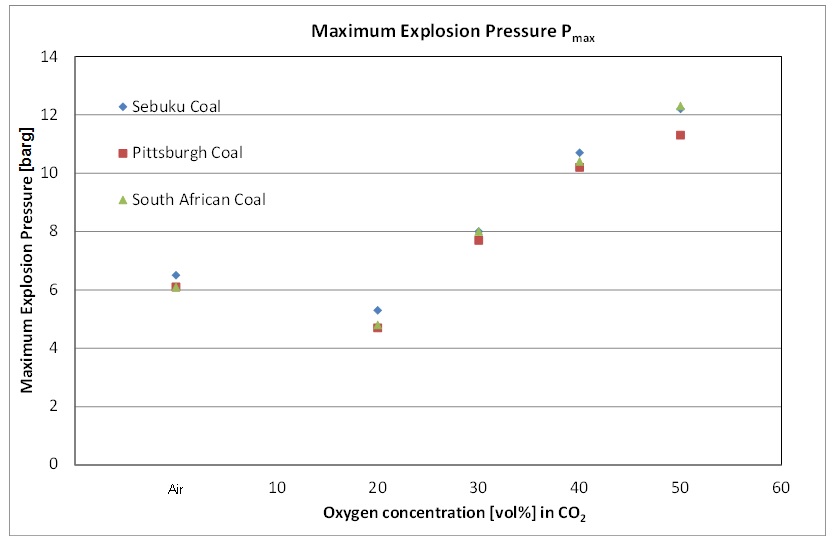
Figure 2: The maximum explosion pressure of the different coals in oxy-fuel atmospheres
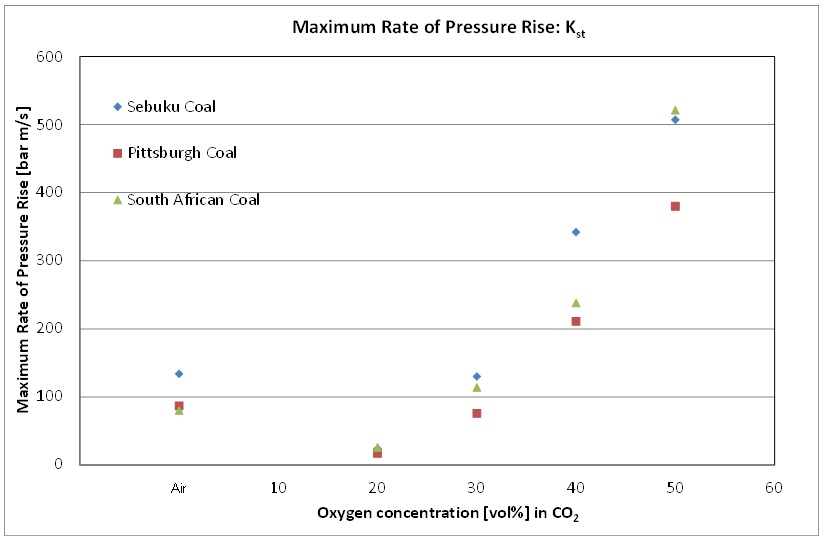
3. Conclusions
It has been proven that both ignition sensitivity and severity in oxy-fuel combustion of coal increase with increasing oxygen concentration. For a concentration around 30 vol.% O2 in CO2 the results are comparable to those obtained in air. For higher concentrations of oxygen e.g. 40-50 vol.% in CO2 coal dusts become very to extremely sensitive for ignition and the explosions are very violent to extremely violent.
Because explosion risk is the product of explosion sensitivity and explosion severity it can be concluded that the dust explosion risk in oxy-fuel atmospheres with an oxygen concentration of 30 % (in CO2) is similar to that in air.
In order to safely operate an oxy-coal fired power plant, i.e. with no additional explosion risk with respect to an air fired plant, the oxygen concentration needs to be limited to 30%. Increasing the oxygen concentration above this value increases both the explosion sensitivity and severity and in such a case extra preventive and protective explosion safety systems would need to be implemented.
Sources
[1] Eckhoff R.K,. Dust Explosions in the Process Industries, 3rd edition, Gulf Publishing Elsevier, Boston, United States, ISBN-10: 0750676027, 2003.
Acknowledgements
The research leading to these results has received funding from the European Community’s Seventh Framework Programme (FP7/2007-2013) under grant agreement n° 268191.