-
What is the effect of combustion air preheat upon process efficiency?
Date posted:
-
-
Post Author
dev@edge.studio
1. Why preheat combustion air?
A substantial margin for energy saving in high temperature furnaces stems from increased thermal efficiency. In a fuel-fired furnace, the flue gases take away from the combustion chamber a large fraction of the heat input as “sensible heat” at temperature tflue. This large loss can be substantially reduced either by means of oxygen firing (hence reducing the quantity of flue gases by a factor of up to four times) or by using the outgoing hot flue gases to preheat the combustion air up to a temperature tair. By so doing, a fraction of the heat in the flue gases is recovered and returned to the combustion chamber.
2. What effect does air preheating have on thermal efficiency?
Defining the air preheating “effectiveness” as the ratio x = tair / tflue, the thermal efficiency hth of a heating process may be calculated by undertaking a heat or energy balance. In Figure 1, the thermal efficiency is shown as a function of flue gas temperature for several values of the effectiveness of the air preheat and for 10% [GLOSS]Excess air[/GLOSS] (lambda (λ) = 1.1) firing natural gas. For the purposes of this Combustion File, only sensible heat losses through the flue have been taken into account in calculating the thermal efficiency.
As can be seen from Figure 1, substantial energy savings are available by air preheating (compare curves for x = 0 and x = 40%, the latter figure being representative of current central [GLOSS]Recuperator[/GLOSS] technology). Doubling the x ratio from 40 to 80 % almost doubles the energy saving, but requires an alternative approach to air preheating (see below). Figure 1 may be used to estimate the improvements in thermal efficiency that can be made from applying an air preheater of known effectiveness to a process having a given flue gas temperature. Similar diagrams can be set up for different excess air factors and different fuels.
It may be noted from Figure 1 that an effectiveness of 100%, even if practically achievable, would not lead to a thermal efficiency of 100%. This is due to the lower heat capacity of the incoming combustion air compared to the outgoing combustion products. The combustion air is simply incapable of absorbing all the sensible heat in the flue gases it creates.
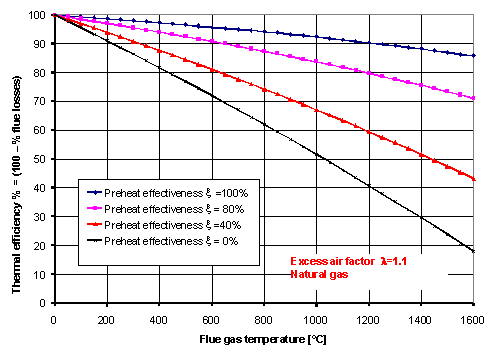
Figure 1 – Thermal efficiency vs flue gas temperature
3. What are the options to preheat the combustion air?
A range of metallic and ceramic heat exchangers is available for use on industrial furnaces. Their effectiveness x in air preheating is generally no higher than 40%. Nevertheless, as can be seen from Figure 1, their deployment on a furnace currently not using preheated air may increase process efficiency substantially.
At a typical flue gas temperature tflue = 1200 °C found on a high temperature furnace, doubling x from 40% to 80% would increase the air preheat from tair ~ 500° to ~ 1000 °C, and increase the thermal efficiency from 60% to 80%. However, such air preheats are intolerably high for conventional central air preheaters attached to the flueways. In addition, it is not possible to distribute air this hot in metallic manifolds to several burners equipping a typical furnace. Therefore, burners have been developed with integral recuperators and regenerators.
Auto-recuperative burners
In an auto-recuperative burner, the counter-current flue-gases/air heat exchanger, embedded inside the burner body, preheats the combustion air close to the burner nozzle. Air is delivered to the burners at room temperature and flue gases are extracted through each burner when they are already cooled down to a few hundred degrees °C. Such burners require appropriate grades of heat resistant materials for components located at the furnace-end of the burner.
The heat exchangers can be manufactured in metal or in ceramic (SiC) and often have an enhanced transfer surface (fins, corrugated ripples etc). An example of a recuperative burner is given in Figure 2. The arrangement shown below is suitable for thermal inputs up to a few hundred kW. In general, recuperative burners can offer air preheat effectiveness x of up to 60% or more.
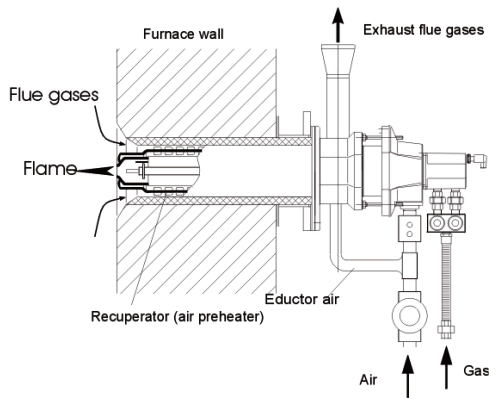
Figure 2 – “Auto-recuperative” burner (after WS GmbH)
Regenerative burners
A very effective solution in terms of air preheating is the [GLOSS]Regenerative burner[/GLOSS]. In such devices, the recuperator is replaced by a compact reversing [GLOSS]Regenerator[/GLOSS]. Effectiveness x goes up to 80% or higher in some designs. Air preheats can reach or exceed 1100°C on high temperature plants leading to substantial energy savings (see Figure 1).
4. Are there drawbacks to using high preheat?
If very high combustion-air preheats are deployed on conventional burners, there are two principal drawbacks:
- The areas of the burner exposed to the preheated air or the flame may reach temperatures higher than their maximum design service temperature, with the consequence of material failure. For this reason, special burners are required that use appropriate grades of heat resistant materials for components located at the furnace-end of the burner. Modern ceramic materials are often employed.
- Unacceptably high [GLOSS]Thermal NO[/GLOSS] will be produced in conventional burners, due to extremely high flame peak temperatures. Therefore, special combustion techniques are required to reduce NOx formation with high temperature air, including [GLOSS]Staged combustion[/GLOSS] and/or flue gas recirculation. In particular [GLOSS]Flameless combustion[/GLOSS] (see CF171) techniques result in very low NOx levels (CF174) while exploiting the large energy saving potential of high air preheat. Flameless combustion also reduces the thermal stress at the burner nose.
Sources
[1] Wünning J., Flammenlose Oxidation von Brennstoff mit hochvorgewärmter Luft, Chem.-Ing.-Tech. 63 (1991)
[2] Flamme M. Boß M., Brune M. et. al., Improvement of Energy Saving with New Ceramic Self-Recuperative Burners, IGRC, San Diego, 1998
[2] R. Weber: Combustion of natural gas, oil and coal with air preheated to temperature in excess of 1000°C – 4th HTACG Symposium, Rome 26-28 November 2001me of