-
What is the current status in the development of “gas reburn” for NOx control in fossil fuel fired furnaces?
Date posted:
-
-
Post Author
espadmin
1. Background
Gas over coal reburning is a comparatively new [GLOSS]NOx[/GLOSS] reduction technology, which combines the principles of air and fuel staging. In this technique already formed NO reacts with hydrocarbon radicals to form atmospheric nitrogen.
In theory any hydrocarbon fuel could be used as the reburn fuel, but there are a number of benefits in using natural gas (Macphail et al, 1997).
In this process, a portion of the total fuel fired to the boiler, in this case natural gas, is injected directly in the combustion gases emanating from the primary combustion zone to create a fuel rich reduced atmosphere. In this example, the remainder of the fuel fired is pulverised coal.
2. Description of the process
2.1 Overview
The process is based upon the staged addition of the air and fuel within the furnace to produce conditions, which are conducive to NOx reduction. In general terms the process can be described thus:
- A primary zone in which the main proportion of the fuel (e.g. coal or oil), typically 80% of the thermal input, is fired in a globally oxidising environment (stoichiometry typically 1.12).
- A secondary zone (known as the reburn zone) where the remainder of the thermal input (20%) is introduced as reburn fuel (i.e. natural gas) without any additional air, so as to create a reducing region (stoichiometry typically 0.9) where NOx created in the primary zone is destroyed.
- A burnout zone where overfire air is added to complete the combustion process.
The processes are shown in figure 1:
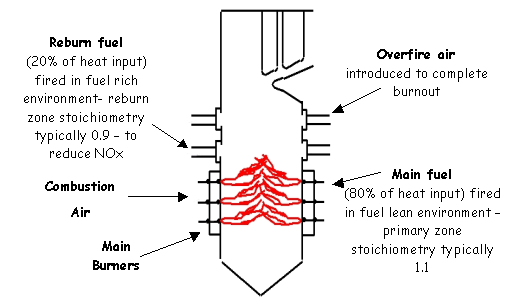
Figure 1: Schematic of a furnace designed with the Reburn Technology.
2.2 Primary zone
The chemical processes occurring in the primary zone are the same as those of conventional coal combustion. However, compared to single stage (baseline) combustion the primary zone is operated at relatively low excess air (thus reducing fuel NOx), and at reduced load (thus lowering temperatures and hence giving reduced thermal NOx). It is also considered that the best overall system performance is achieved with the lowest possible NOx formation in the primary zone, and so ideally [GLOSS]LNB[/GLOSS] should also be installed for the main fuel combustion, (see CF127).
Residence time in the primary zone should be sufficiently long essentially to complete the combustion of the main fuel. Any unburned fuel will pass through the reburn zone and continue burning in the burnout zone. In the oxidising atmosphere of the upper furnace any remaining char nitrogen will be released in a region that is conducive to its conversion to NOx, and as a result the overall NOx reduction efficiency of the gas reburn process will be diminished.
2.3 Reburn zone
In the reburn zone the natural gas is decomposed into hydrocarbon radicals (CHi) rather than undergoing combustion, as a result of the oxygen deficient conditions in this region. These hydrocarbon radicals react with NOx that was produced in the primary zone to give HCN, which feeds back into the overall NOx formation/reduction process.
With a reducing stoichiometry the conditions favour the reaction paths leading to N2 in preference to those giving NOx. In effect the hydrocarbon radicals act to destroy previously produced NOx, unlike air staging processes where the aim is simply to minimise the formation of NOx. The residence time in the reburn zone must be sufficient for the mixing of the natural gas and bulk flue gas to be completed, and the gas phase reactions to occur.
2.4 Burnout zone
The burnout zone is where the addition of overfire air raises the overall stoichiometry to allow the combustion process to be completed – it is essentially the same as the burnout zone in furnace air staging processes.
3. Key parameters of the process
The controlling parameters of the process are the reburn zone stoichiometry, temperature and residence time. The effectiveness of the process depends also on the type of reburn fuel and specifically, on its reactivity and nitrogen content.
Other important parameters are main combustion zone residence time and temperature, primary NO level and dispersion and mixing of the reburning fuel and of the burn out air.
Because the main flow of the gas is small compared to the total furnace flow, mixing of the gas across the full depth of the furnace (i.e. achieving adequate penetration) is difficult. Early applications of reburn technology therefore used recycled flue gas as a means of boosting the momentum of this stream (this process is described in CF131). The quantity of flue gas required is large (typically 6% of the full furnace flow) and the [GLOSS]FGR[/GLOSS] fans for this purpose require considerable auxiliary power.
The use of FGR for mixing of the reburn gas is expensive; it adds significantly to the capital cost of the system and the operating costs, and the FGR fan is potentially a high maintenance item due to the risk of fan blade erosion. Ideally the mixing would be accomplished without the need for FGR.
4. What would a typical installation include?
A typical installation of gas reburn would include the following items:
- LNB’s – minimising the primary NOx is beneficial to the process as a whole.
- Reburn gas supply system, [GLOSS]C & I[/GLOSS].
- Reburn gas injectors.
- Booster fan.
- Overfire air injectors.
- Upgrades to C & I, control philosophy.
- Upgrades to milling plant.
It is seen from the above that the scope of supply is comprised largely of standard equipment with a well-proven track record in utility applications.
Positioning of the reburn gas injectors and overfire air nozzles is largely dependant upon the constraints of the existing plant. The usual approach in a retrofit situation is to identify the most practical elevation for the reburn injectors and overfire air nozzles that best matches the process requirements, and then to optimise the lateral positioning on the basis of CFD modelling – often access to the rear wall of the furnace is obstructed and a compromise must be made to arrive at the best mixing performance subject to the existing constraints.
Similarly in a retrofit situation the height of the existing furnace will impose a constraint on the available residence time. With the requirement to achieve acceptable carbon in ash, fixing the burnout zone residence time (which can be shortened if the benefits of mill upgrading can be taken into account for coal fired plant) it is usual for the NOx performance potential to be compromised.
5. What are the advantages of gas reburn?
Gas over coal reburning is a comparatively new technology, which combines the principles of air and fuel staging. In theory any hydrocarbon fuel could be used as the reburn fuel, but there are a number of benefits in using natural gas (Macphail et al, 1997), these are summarised as follows:
- Good mixing characteristics and easily controlled.
- Quick formation of species involved in NOx reducing reactions. With natural gas all the hydrocarbons are immediately available for reaction, thus maximising the effectiveness of the residence time in the reburn zone.
- Limited effect on boiler performance.
- Comparatively easy to retrofit, particularly when space is limited (no additional fuel preparation is required).
- No on-site storage of potentially hazardous chemicals.
- Good load following characteristics.
- Minimal fouling.
- Minimum impact on burnout. Natural gas has no fixed carbon which needs residence time in the burnout zone.
- Lower SO2 emissions. SO2 is reduced in proportion to the amount of natural gas fired.
- Reduced CO2 in the flue gas, due to the lower C :H ratio in natural gas.
- Reduced ash disposal.
- No fuel nitrogen (which could potentially be converted to NOx in the burnout zone).
However the use of natural gas is dependant upon its local availability on site. The capital costs of installing a pipeline are significant and gas reburn is only economically attractive when the natural gas main grid distribution network passes reasonably close to the candidate site. In addition the cost premium of natural gas compared to the coal it displaces can add a significant economic burden, and gas supplies can be volatile.
Sources
[1]Michelfelder S & Leikert K. The Stage Mixing Burner and Operating Results of Pulverised Coal Burners for Low NOx Emission. VGB Kraftwerkstechnik 60 (2) 95-103. (1980)
[2]Lam KB, Wilkinson PJ & King JL. Application of Low NOx Axial Swirl Burners to Castle Peak B Power Station. 9th CEPSI Conference – Hong Kong. (1992)
[3]Macphail J, Rhine JM & Hughes M. The Demonstration of Gas Reburning Technology on a 600 MWe Boiler at Longannet, Scotland. (1997)
[4]Macphail J, Rhine JM & Hughes M. Proceedings “4th International Conference on Technologies and Combustion for a Clean Environment”, Scotland. (1997)
[5]Hesselmann G & Chakraborty R. Coal Over Coal Reburn – The Applicaton of Pilot Scale Test Results to Utility Plant Design. Power-Gen Europe 98. (1998)