-
What are the lime and dead burnt dolomite processes?
Date posted:
-
-
Post Author
dev@edge.studio
1. Introduction
The complete range of processes undertaken in the minerals processing industry was outlined in CF 255. This combustion file gives more specific detail of the processes in use for the manufacture of lime and dead burnt dolomite.
2. Lime & Dead Burnt Dolomite
[GLOSS]Limestone[/GLOSS] production is the largest tonnage industry in the world, and is geographically diverse. Of this, approximately 10% is converted to [GLOSS]lime[/GLOSS]. It is unusual for bulk lime, or lime products to be transported more than 100km from its point of production, as it is a low value product (~60$/tonne 1994 USA), and there are therefor a large number of lime plants worldwide. Figure 1 shows the split of annual world lime manufacture by continents for 1977, which is not significantly different to the current status of the market in both distribution and quantity (viz. 150 million t.p.a. in 1994).
Approximately 25% of the annual world lime production is generated by rotary kilns, with the largest concentration of rotary kilns being in North America (~80% of US annual production). The selling price of lime is low, and thus the marginal profit on lime is small. This is more critical for a [GLOSS]rotary kiln[/GLOSS], where the specific fuel consumption is between 4.8 – 6.0 MJ/kg, depending on the [GLOSS]preheater[/GLOSS] system, compared to 3.0 – 4.5 MJ/kg for a good [GLOSS]shaft kiln[/GLOSS]. Even in the USA, which is a traditionally low cost fuel nation, the average cost of energy is approximately 50% of the gate-selling price of lime.
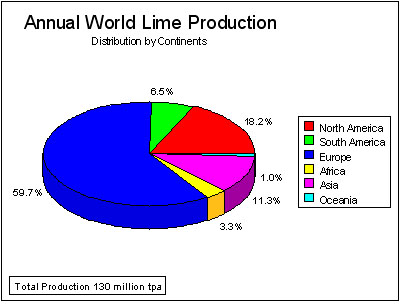
Figure 1 World Lime Production for 1977 (Boynton)
The advantage of a rotary kiln is its ability to process small stone (<30mm) to dust, which is not suitable for a shaft kiln due to bed blinding. The quarrying and crushing of limestone will typically produce only about 40% of ‘large’ shaft kiln stone, and unless there is a market for the small stone as aggregate, the undersize stone presents a major cost penalty to the quarry operation. It is therefor quite common to find both shaft and rotary kilns at the same site, thereby maximizing the utilization of the quarry. For large tonnage demands to a captive market, e.g. steel, it may be justifiable to build one large rotary kiln, rather than a battery of smaller shaft kilns, but this may also be governed by the quality requirements.
Lime quality is specifically tailored to its markets with respect to the [GLOSS]reactivity of lime[/GLOSS] (with water); retained sulphur (low requirement for steel); ‘[GLOSS]available lime[/GLOSS]’ ([GLOSS]calcination[/GLOSS] efficiency); SiO2 impurity (low requirement for soda ash, steel, alumina); heavy metal content (very low requirement for pharmaceuticals); and flue gas CO2 content (for precipitated calcium carbonate (PCC) and soda ash production); thus the actual operation of the kiln becomes more of an art than a precise science and is highly dependent on the [GLOSS]burning zone[/GLOSS] conditions.
The word limestone is used in a generic sense to mean any rock with a high calcium carbonate content, which also includes chalk, coral, and sea sand. High purity limestone (>95% CaCO3) is required to produce commercial lime, but also included in the analysis of this market is the production of dead burnt dolomite, which is a ~60%CaO/40%MgO material. This is heated to a higher temperature than lime in order to yield an unreactive ([GLOSS]dead burnt[/GLOSS]) product, which is used for refractory, and thus has a higher specific fuel consumption. Most dead burnt dolomite is produced in rotary kilns.
3. Lime for Pulp & Paper
Lime is required for the production of wood pulp, where it is used to re-causticize sodium hydroxide (used for primary digestion of the wood chips). In this case, Ca(OH)2 ([GLOSS]slaked lime[/GLOSS]) is reacted with Na2CO3 to yield CaCO3, which is then recycled as a filter cake to the kiln to regenerate CaO. During this process, the lime becomes ‘diluted’ by other minerals from the digested wood. The recycled material is therefor different in character to pure limestone, building coatings and rings on the kiln wall (akin to cement manufacture described later). The nature of the ‘[GLOSS]lime mud[/GLOSS]’ feed to the kiln means that almost all lime re-burning (>95%) is carried out in a basic rotary kiln. Most pulp mills have between one and three kilns, typically producing 300-400 tpd/kiln with a specific fuel consumption of 5.5 – 6.5 MJ/kg.
Pure limestone is only used to ‘top-up’ the feed to the kiln to maintain an adequate percentage of free lime in the product. The lime produced is recycled and internally consumed in the pulp mill, it is therefor not easy to quantify the annual production of lime in this market sector, but there are of the order of 500 pulp mills worldwide. This would equate to 50-100 million t.p.a. of lime. The non-primary function of the lime mud kiln (i.e. it is not sold as product, and is not in the critical paper manufacturing path) results in a lower plant profile for investment. However, it is important to recognize that the kiln is the primary user of imported fuel and purchased raw materials (limestone), since the wood is normally owned by the mill and the waste products from the wood provide fuel for the rest of the plant’s power and steam requirements. These kilns are also often used as incinerators to dispose of noxious or explosible vent gases (H2S, light volatiles, etc.), and waste liquids (turpentine, methanol, etc.).
Sources
[1] Boynton R S, Chemistry and Technology of Lime and Limestone, John Wiley & Sons, 1980, ISBN 0-471-02771-5