-
What are high emissivity furnace wall coatings, and how effective are they?
Date posted:
-
-
Post Author
dev@edge.studio
1. What is a high emissivity coating?
Any coating applied to a surface with the intention of increasing its [GLOSS]emissivity[/GLOSS] (Combustion File 92) without materially affecting the structure of the material (‘substrate’) to which it is applied, can be said to be a high emissivity coating. They are generally thin coatings that are sprayed or brushed onto the surface. They have been applied to both metal surfaces, where they can also provide protection against corrosion, and to the refractory walls of furnaces. In the latter case they may also be applied to seal cracks and gaps in damaged brickwork.
Because of the temperatures to which they are exposed, high emissivity coatings are usually ceramic coatings, which comprise of materials such as alumina-silica, zirconia or silicon carbide with propriety constituents added which are claimed to give the coating its high emissivity.
Since the early 1980’s a number of companies have been selling high emissivity coatings for application on furnace walls and have published claims of significant energy saving. A number of claims for their effectiveness have been published including [1]:
– A 22.5% energy saving on a pit type furnace with a 67.5% improvement in temperature uniformity
– A 10% reduction in energy use on annealing furnaces with an 18% reduction in heat up time
– An average reduction in energy use on aluminium bale out furnaces of from 110 [GLOSS]therm[/GLOSS]s to 70 therms per shift following coating of the hot face of the refractory
High emissivity coatings are also quite commonly applied to the hot face of the radiant section of fired heaters in petrochemical plant.
There exists considerable scepticism about these coatings. There is firstly a general belief that uncoated furnace refractory materials are of high emissivity on account of their rough physical surface structure (CF150). Also, it is often argued that in a closed chamber, radiation from the insulating walls is either reflected or emitted, so that the chamber effectively behaves like a [GLOSS]black body[/GLOSS] furnace; the emissivity of the refractory should therefore not affect the net heat transfer to the load [2]. Theoretical studies, however, have demonstrated that improvements in heat transfer are possible.
2. How does a high emissivity coating work?
In a gas or oil fired furnace, the high temperature non-luminous and non-grey combustion gases absorb and emit radiation at discrete wavelengths corresponding to the spectra for the CO2 and H2O molecules (CFs 96, 97). Of particular interest are the ‘windows’ in the spectrum through which radiation can pass unattenuated, Fig.1.
Radiant energy from the hot gases that is reflected off the wall surface, does not change its wavelength and hence can be significantly absorbed by the gas before reaching the load surface. Radiation that is absorbed by the wall on account of its emissivity is re-emitted. A proportion of this energy can pass unattenuated through the ‘windows’ in the gas spectra.
If the wall is ‘black’ or of a high emissivity, then more radiation is able to reach the load surface without re-absorption by the gas. Thus a net redistribution of energy occurs across the spectrum resulting in an increase in heat transfer to the load.
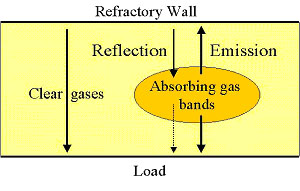
Fig.1 The radiation interchange between a non-grey gas and refractory and load surfaces in a furnace.
3. By how much is emissivity increased?
There are no reliable and independent published data on the emissivity of these coatings. One supplier claims that the emissivity of their coating is higher than 0.92 and remains above this level for temperatures up to 1650oC, whereas the emissivity of normal refractory materials decreases significantly at high temperatures (CFs 147,148, 223, 224).
Reliable data on the emissivity of alumina-silica does show emissivity decreasing with temperature Fig.2, [3]. These data are also supported by spectral emissivity measurements which show that emissivity below 2 micron is less than 0.3, Fig.3. Thus, as temperatures increase, the total emissivity decreases because of the shift in radiant emission towards lower wavelengths. Thus, the emissivity of refractory materials may indeed be lower than expected adding credence to the possibility that coatings may actually increase wall emissivity significantly. However, it is also yet to be verified whether high emissivities can be maintained over time in a real working furnace environment.
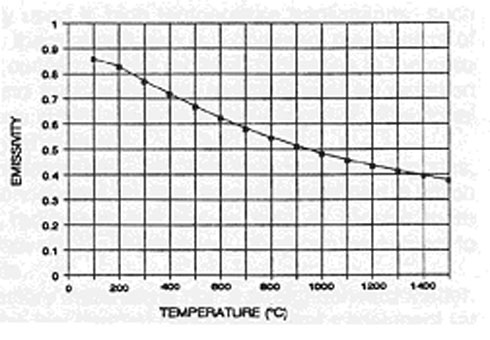
Fig.2 – The total emissivity of an alumina-silicate refractory and its variation with temperature [3].
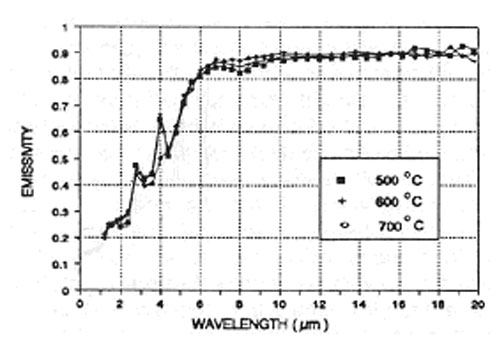
Fig.3 – The spectral emissivity of an alumina-silicate refractory [3].
4. What is the predicted benefit of increasing emissivity?
As explained above, improvement in the radiant heat transfer in furnaces can only occur on account of the non-grey nature of the gases. Simple mathematical models that assume a [GLOSS]grey gas[/GLOSS] (CF95) or that no absorbing gas is present, usually show no effect on performance when emissivity is increased.
Zone models using the weighted sum of grey gas model for combustion products (CF44), allow for non-grey behaviour and in particular the effect of ‘windows’ in the spectrum. Independent work by Leeds University[4] and by British Gas [5] came to the same conclusions – that models can predict improvements in heat transfer, when wall emissivity is increased, but only if non-grey gas behaviour is taken into account. The level of improvement depends on many other factors such as the original furnace efficiency, the emissivity of the load, the temperature, the conductivity of the wall, and whether a steady-state or a transient model is being applied. Docherty and Tucker [5] showed that the effect is more significant for steady-state processes when wall heat loss is insignificant. For example, on a steady-state steel reheating furnace of efficiency 46% , a fuel saving of 4.6% was predicted when emissivity was increased from 0.5 to 1.0. For transient processes, the increase in emissivity can lead to an increase in heat absorption and loss into the wall, reducing or eliminating the benefits.
The weighted sum of grey gases model is however not a true physical representation of the banded nature of the gas radiation. More detailed and rigorous models are required. Coventry University has published results from a single zone model that allows for the individual absorption bands of CO2 and H2O [6]. This model predicted similar decreases in fuel input to maintain a given load heat transfer, when emissivity is increased from 0.5 to 0.9.
5. What experimental evidence on the effectiveness of high emissivity coatings exists?
Little independent experimental evidence has been published, and none showing conclusive evidence that the coatings provide an enhancement in performance. Experimental work by Leeds University[4] and by British Steel has concluded that the enhancement is marginal or insignificant. However, if the effects are small (<5%), they will be difficult to detect due to the experimental errors associated with experimental heat transfer measurements on furnaces. In addition, in real production situations, there are larger uncertainties in measuring and comparing fuel consumption before and after furnace coating.
6. What should a prospective user of high emissivity coatings conclude?
q Theoretical models support the claims that furnace efficiency should increase if wall emissivity is increased on fuel-fired furnaces.
q There is reliable data showing that the emissivity of standard refractory surfaces, particularly at high temperatures, can be less than 0.5.
q There is a dearth of data on the emissivity of coatings
q There is no evidence that high emissivity is actually maintained during service.
q The extent of the benefits claimed for these coatings remain unsubstantiated by any independent scientific analysis.
q Some of the energy saving claims published by the suppliers may indeed arise due to other associated benefits. For example, the coatings may help to seal cracks and gaps in old refractory brickwork.
q The low cost of application of coatings may quite possibly result in short term pay back on investment even when benefits are not as high as those sometimes claimed
Sources
1. John Hellander, ‘Ceramic Coatings: Function and Documented energy and Maintenance Savings, Industrial Heating, p30, Sept.1986
2. Symposium Report ‘The emissivity of furnace materials and its effect on plant performance’, Energy World, November 1985.
3. Jackson J.D., Yen C.C., An P., Some measurements of the total and spectral emissivity of a refractory material, Proc.Eurotherm Seminar 21 on Heat Transfer in Semi-Transparent Media, Villeurbanne, Lyon, 3-5 Feb 1992, pp29-38.
4. Elliston D.G. et al., ‘The effect of surface emissivity on furnace performance’, J.Inst.Energy, Dec 1987, pp155-167.
5. Docherty P., Tucker R.J., The influence of wall emissivity on furnace performance, J.Inst.Energy, March 1986.
6. Khan Y.U., Lawson D.A., Tucker R.J., Analysis of radiative heat transfer in ceramic lined and ceramic coated furnaces, J.Inst Energy, 1998, 71, pp 21-26.