-
How is Coke Oven Gas produced?
Date posted:
-
-
Post Author
dev@edge.studio
1. Introduction
The typical fuel gases used in integrated iron and steelworks are listed in CF62 and introduced in more detail in CF100. This group of industrial fuel gases includes [GLOSS]Coke Oven Gas[/GLOSS] or [GLOSS]COG[/GLOSS].
COG is produced as a by-product from [GLOSS]coke[/GLOSS] production. Coke is used in [GLOSS]blast furnaces[/GLOSS] for the production of pig iron or “[GLOSS]hot metal[/GLOSS]”. To make coke, [GLOSS]coal[/GLOSS] is heated in the absence of oxygen to drive off the volatile matter.
COG is a valuable by-product since it can be used as gaseous fuel in various applications inside or outside the steel plant. One of the biggest consumers is the coke plant itself, where up to 50% is used as the coke plant fuel.
The fuel properties of COG, its combustion and flue gas properties, and its applications are described in associated Combustion File numbers 239, 240 and 241 respectively.
In the present combustion file the production processes of COG are described. A coke plant consists of a coal supply system, one or more coke batteries, a coke quenching system and a coke oven by-product plant. These are described in more detail below.
2. The Coke Battery
A coke battery is shown in Figure 1. Every battery consists of a number of coke ovens, separated by combustion chambers.
A coke oven is a long, narrow and relatively high space with typical dimensions:
q Length=15 meters
q Height=5 meters
q Width=0.5 meters
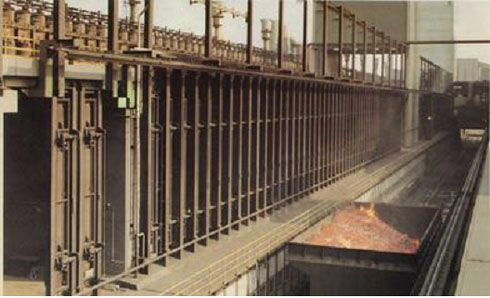
Figure 1. A typical coke battery
The coke oven is filled with [GLOSS]bituminous coal[/GLOSS], following which the newly filled coke oven is sealed to prevent leakage of air into the oven.
The coal is then heated to a temperature of about 1000°C by heat transferred from the surrounding combustion chambers.
The water content of the coal starts to evaporate and the volatile fraction of the coal is liberated.
The coal softens and the granular solid coal changes into a plastic mass, which finally transforms into a hard, coherent, porous coke mass.
3. The Coking Process
Inside a coke oven, the coal to coke process takes place as follows:
· Firstly the coal softens at the walls of the coke oven.
· As the temperature in the coke oven increases, this layer becomes thicker, raw COG is generated and the pressure increases.
· When the two layers meet in the centre, a pressure peak is generated. The coke breaks up into smaller pieces during the late stages of the coking cycle.
The coal to coke production cycle takes about 20 hours. After this period the coke is pushed out of the oven and transported to a quench station, where the coke is rapidly cooled (either with water or nitrogen). Figure 2 shows incandescent coke in the oven waiting to be pushed out.
Figure 2
Coke in the oven waiting to be pushed out
3. Coke oven gas recovery and cleaning
Raw COG leaves the coke oven chambers as hot gas containing ash particles, heavy [GLOSS]hydrocarbons[/GLOSS], light hydrocarbons, amines, sulphates and water vapour. Before this gas can be used as fuel it first needs to be treated:
q The gas needs to be cooled to condense out water vapour and contaminants
q The [GLOSS]tar[/GLOSS], naphthalene and solid aerosols need to be removed to prevent gas line and equipment fouling.
q Light oil needs to be removed and recovered for sale of benzene, toluene and xylene
q Ammonia needs to be removed to prevent gas line corrosion and excessive [GLOSS]NOx[/GLOSS] formation during combustion of COG
q Hydrogen sulphide and hydrogen cyanide need to be removed to meet local emissions regulations governing the combustion of COG.
These processes are undertaken in the coke by-product plant.
Historically, the by-product chemicals were of high value in agriculture and in the chemical industry, and the profits made from their sale were often of greater importance than the coke produced.
Nowadays however, most of these products can be more economically manufactured using other technologies such as those of the oil industry.
Therefore, with some exceptions depending on local economics, the main emphasis of a modern coke by-product plant is to treat the coke oven gas sufficiently so that it can be used as a clean, environmental friendly fuel.
Sources
[1] American Iron and Steel Institute, www.steel.org.
[2]Wilson, H. Fuels and Combustion, Reheating Technical Course.
[3] Militzer, M.R., UEC Coal & Coke Laboratory, Coke Production for Blast Furnace Ironmaking.
[4] Valia, H.S. Coke production for blast furnace ironmaking, Ispat Inland Inc, American Iron and Steel Institute.
[5] Platts, M. The coke oven by-product plant, ThyssenKrupp EnCoke, American Iron and Steel Institute.