-
How is Blast Furnace Gas (BFG) produced?
Date posted:
-
-
Post Author
dev@edge.studio
1. Introduction
The typical fuel gases used in integrated iron and steelworks are listed in CF62 and introduced in more detail in CF100. This group of industrial fuel gases includes [GLOSS]Blast Furnace Gas[/GLOSS] or [GLOSS]BFG[/GLOSS].
Blast Furnace Gas is produced as a by-product from pig iron production in [GLOSS]blast furnaces[/GLOSS]. Pig iron, or “[GLOSS]hot metal[/GLOSS]” is a base material for steel production in a basic oxygen furnace or an electric arc furnace.
Blast Furnace Gas is a low [GLOSS]calorific value[/GLOSS] fuel gas, which can be used as gaseous fuel in various applications inside or outside the iron making plant. A significant amount of Blast Furnace Gas is used for the production of hot blast in blast furnace stoves.
The fuel properties of BFG, its combustion and flue gas properties, and its applications are described in associated Combustion File numbers 242, 243 and 244 respectively.
The present CF concentrates on BFG production, but to do so it is first necessary to understand the basics of iron production.
2. Production of Iron in Blast Furnace
The purpose of a blast furnace is to chemically reduce and physically convert iron oxides into liquid iron. As by-products, [GLOSS]blast furnace slag[/GLOSS] and Blast Furnace Gas are generated. The processes taking place in a blast furnace are described in numerous textbooks and articles. A good, comprehensive description is given in the article “How a blast furnace works”, written by John A. Ricketts [2]. In this section, this article is used to describe the production of Blast Furnace Gas.
A blast furnace, see Figure 1, is a large, vertical, refractory lined steel vessel, into which iron ore, [GLOSS]coke[/GLOSS] and [GLOSS]limestone[/GLOSS] are charged into the top, and preheated air, sometimes enriched with pure oxygen, is blown into the bottom. A part of the coke may be replaced by [GLOSS]coal[/GLOSS] injection at the bottom of the blast furnace.
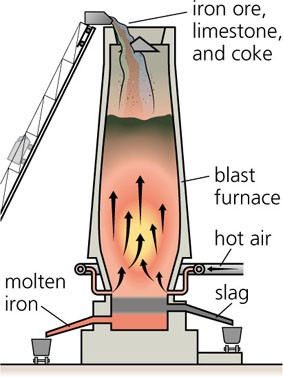
Figure 1 Basic Concept of Iron Production in a Blast Furnace
The raw materials require 6 to 8 hours to descend to the bottom of the furnace where they become the final product of liquid slag and liquid pig iron. These liquid products are tapped from the furnace. The hot air that was blown into the bottom of the furnace ascends to the top in 6 to 8 seconds after going through numerous chemical reactions. A typical blast furnace will operate almost continuously for 6 to 10 years, producing 3 000 to 12 000 tons of liquid iron each day, depending upon its size.
Iron oxides can come to the blast furnace plant in the form of raw ore, pellets or sinter. Raw ore is either Hematite (Fe2O3) or Magnetite (Fe3O4) and the iron content ranges from 50% to 70%. Once these materials are charged into the furnace top, they go through numerous chemical and physical reactions while descending to the bottom of the furnace. The iron ore, pellets and sinter are reduced, which simply means the oxygen in the iron oxides is removed by a series of complex chemical reactions that take place at high temperatures. The reactions can be summarised by the following global reactions that occur as follows:
3 Fe2O3 + CO ® CO2 + 2 Fe3O4 |
Begins at 450 °C |
Fe3O4 + CO ® CO2 + 3 FeO |
Begins at 600 °C |
FeO + CO ® CO2 + Fe |
Begins at 700 °C |
At the same time the iron oxides are going through these purifying reactions, they are also beginning to soften then melt and finally trickle as liquid iron through the coke to the bottom of the furnace. The coke descends to the bottom of the furnace to the level where the preheated air or hot blast enters the blast furnace. The coke is ignited by this hot blast and immediately reacts to generate heat as follows:
C + O2 ® CO2 + Heat
Since the reaction takes place in the presence of excess carbon at a high temperature the carbon dioxide is reduced to carbon monoxide as follows:
CO2+ C ® 2 CO
The product of this reaction, carbon monoxide, is necessary to reduce the iron ore as seen in the previous iron oxide reactions. The limestone descends in the blast furnace and remains a solid while going through its first reaction as follows:
CaCO3 ® CaO + CO2
This reaction requires energy and starts at about 900 °C. The CaO formed from this reaction is used to remove sulphur from the iron, which is necessary before the hot metal becomes steel. This sulphur removing reaction is:
FeS + CaO + C ® CaS + FeO + CO
The CaS becomes part of the slag. The slag is also formed from any remaining Silica (SiO2), Alumina (Al2O3), Magnesia (MgO) or Calcia (CaO) that entered with the iron ore, pellets, sinter or coke. The liquid slag then trickles through the coke bed to the bottom of the furnace where it floats on top of the liquid iron since it is less dense.
3. Production of Blast Furnace Gas
An important by-product of the iron making process is hot Blast Furnace Gas. Every cubic meter of hot blast air becomes approximately 1.35 cubic meter of Blast Furnace Gas discharged from the top of the furnace. The Blast Furnace Gas proceeds through gas cleaning equipment where particulate matter is removed from the Blast Furnace Gas and it is cooled – See Figure 2
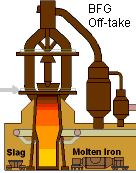
Figure 2 Superstructure of a Blast Furnace Showing BFG Collection System
The composition of blast furnace gas is a result of many, complex chemical reactions taking place inside a blast furnace, some of which were described in Section 2. Blast Furnace Gas typically consists of nitrogen (ca. 50vol.%), carbon monoxide (ca. 20vol.%), carbon dioxide (ca. 20vol%), hydrogen (ca. 3 vol%) and water vapour (ca. 7 vol%).
The hydrogen content of Blast Furnace Gas is mainly dependent on the amount of directly injected powder coal into the bottom of the blast furnace. As described above, powder coal injection can partly replace coke inside the blast furnace. Since coal contains volatile matter, contrary to coke, the amount of hydrogen in the Blast Furnace Gas increases with increasing level of coal injection.
The carbon monoxide content is dependent on the level of oxygen enrichment in the hot blast. The water vapour content is dependent on the temperature of the gas, when it is used in a technical facility, since it is always saturated due to wet scrubbing.
Sources
[1] American Iron and Steel Institute, www.steel.org
[2] Ricketts, J.A., How a blast furnace works, Ispat Inland Inc.
[3] The American Heritage® Dictionary of the English Language: Fourth Edition. 2000.