-
How is a sampling train used to sample trace metals and particulates in flue gases?
Date posted:
-
-
-
Post Author
Patrick LaveryCombustion Industry News Editor
-
1. Background
Background information on trace metals can be found in CF58.
This Combustion File (CF) deals with the use of a sampling train conforming to the requirements of US EPA Method 29: Determination Of Metals Emissions From Stationary Sources, to take samples of a flue gas for the analysis of trace metals and particulates. The preparation of this sampling train, and the cleanup of the sampling train are the subject of CFs 206, 207 and 209.
Safety
This CF does not cover safety procedures. The reader should consult other safety literature and particularly local safety regulations before performing the acquisition of the sample.
Equipment
The equipment used in the acquisition, recovery and cleanup of the sample and sampling train is described in CF206.
2. Sampling Train Use
General considerations:
¨ During sampling, maintain an [GLOSS]isokinetic sampling[/GLOSS] rate (within 10% of true isokinetic)
¨ Maintain a temperature around the filter of 120 ± 14 oC.
For each run, record the sampling information on a data sheet
¨ Be sure to record the initial dry gas meter (DGM) reading
¨ Record DGM readings at the beginning and the end of each sampling time increment, and when there are changes to the flow rate, and before and after each leak check, and when sampling is halted
¨ Take readings of other values (e.g. approx flow rate, wet meter gas volume, wet meter temperature, inlet, outlet and average temperatures, time) at least once for each sampling point
¨ Take additional readings for all parameters when there are significant changes in flow (i.e. 20% variation in velocity head readings)
1. Clean the portholes prior to the test run to minimize the chances of collecting deposited material
2. Verify the filter and probe heating systems are up to temperature (120 ± 14oC)
3. Remove the nozzle cap; verify that the pitot tube and probe are properly positioned
4. Position the nozzle at the first traverse point with the tip pointing directly into the gas stream
5. Immediately start the pump, and adjust the flow to isokinetic conditions
6. When the stack is under significant negative pressure (i.e. height of the impinger stem) take care to close the coarse adjust valve before inserting the probe into the stack to prevent water backing into the filter holder
¨ If necessary, the pump may be turned on with the coarse adjust valve closed
7. When the probe is in position, block off the openings around the probe and the porthole to prevent unrepresentative dilution of the gas stream
8. Traverse the stack cross section (following the traverse points determined – CF204 and 205), being careful not to bump the probe nozzle into the stack walls when sampling near the walls or when removing or inserting the probe through the portholes – this minimizes the chance of extracting deposited material
9. During the test run, make periodic adjustments to keep the temperature around the filter holder at the proper level – add more ice (to the ice bath), if necessary, to maintain temperature below 20oC at the condenser/silica gel outlet
¨ Also periodically check the level and zero of the manometer
10. If the pressure drop over the filter becomes too high (due to the build up of particulates), then replace the filter during the sampling run (to maintain isokineticism)
¨ Change the complete filter assembly rather than adjust the filter itself
¨ Conduct a leak check before it is installed
¨ The total particulate matter (PM) for the sampling run is the sum of all the PM on all the filters used
11. A single train should be used for the entire run, except where simultaneous sampling is required, or if there is an equipment malfunction
12. At the end of the sampling run, close the coarse adjust valve, remove the probe and nozzle from the stack, turn off the pump, record the final DGM meter reading, and conduct the post-sampling leak check
13. Leak check the pitot lines as well:
¨ Blow through the pitot impact opening until at least 7.6 cm H2O velocity registers on the manometer, then close off the impact opening
¨ Criterion: the pressure must remain stable for 15 seconds
¨ Do the same for the static pressure side, except using suction to obtain a minimum of 7.6 cm H2O
14. Calculate the percent isokinetic to ensure that the run was valid (calculation method below). If it was not valid, another run is required.
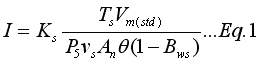
Where: I = percent isokinetic (%)
Ks = 4.320 (metric), 0.09450 (English units) [mmHg/K]
Ts = absolute average stack gas temperature [K]
Vm = volume of gas sample measured by the DGM, corrected to standard conditions [dscm]
Ps = absolute stack gas pressure [mm Hg]
An = cross sectional area of nozzle [m2]
theta = total sampling time [mins]
Bws = water vapour in gas stream [proportion by volume]
vs = stack gas velocity, [m/s] calculated by:
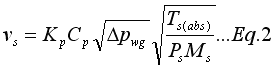
Where:
Kp = 34.97 [(m g/gmole mmHg)/sec K mmH2O]1/2
Cp = pitot tube coefficient [dimensionless]
delta pwg = velocity head of stack gas [mmH2O]
Ts(abs) = absolute stack gas temperature [K]
Ps = absolute stack gas pressure [mmHg]
Ms = molecular weight of stack gas (weight basis) [g/gmole]
If the percent isokinetic is within 10%, then the sample is acceptable, and sample recovery can begin.
Sources
[1] US EPA, US EPA Method 29: Determination Of Metals Emissions From Stationary Sources, US Federal Registry.
[2] US EPA, US EPA Method 2: Determination Of Stack Gas Velocity and Volumetric Flow Rate, US Federal Registry.
[3] US EPA, US EPA Method 5: Determination Of Particulate Matter Emissions From Stationary Sources, US Federal Registry.