-
How do I characterise the combustion properties of black liquor?
Date posted:
-
-
Post Author
espadmin
1. Introduction
[GLOSS]Black liquor[/GLOSS] is a fuel of the [GLOSS]chemical pulping[/GLOSS] industry and has many special features different from other fuels. Standard procedures on chemical and physical analysis have traditionally been developed and performed by pulp and paper research centers in countries producing large quantities of pulp and paper. There is no standard combustion analysis specific for black liquor.
This CF tells which specific black liquor combustion characteristics are available. The methods are not yet standardized and their purpose is to give indications of the behavior of the black liquor in a recovery boiler. Standardized methods (SFS, DIN,….) for other fuels have to be modified if they are used for black liquor.
The combustion characteristics presented in this CF have mainly been developed at Åbo Akademi University and are routinely used on studied black liquor samples. They have been used for about ten years and, therefore, a comparison of the results can be given for various processes and liquors. The purpose has been to perform tests on black liquors in conditions relevant for black liquor recovery boilers. The characteristics can also be used in detailed research work of special topics in combustion (e.g. nitrogen chemistry) and boiler performance studies (e.g. fouling of heat surfaces). Different modifications of the test methods can be available at other research or analytical service laboratories.
The black liquor combustion characteristics that are listed in this CF are:
1) [GLOSS]pyrolysis[/GLOSS] time
2) char combustion time
3) maximum relative swelling
4) volatile carbon
5) fixed carbon
6) SO2 formation tendency
7) NO formation tendency
Purpose
The characteristics can be used for comparing liquors with each other and thereby understanding changes in the recovery boiler performance at pulp mills; or be used for comparing how one type of recovery boiler performs at mills using different liquors. The combustion characteristics can also give indications of changes happening in the liquor that may, for example, cause problematic situations at the recovery boiler. Figure 1 illustrates where these fuel characteristics can be applied in a recovery boiler.
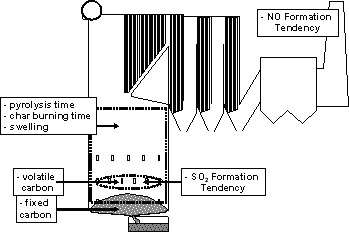
Figure 1. Areas in the black liquor recovery boiler where the combustion characteristics show an effect.
The first three characteristics: 1) pyrolysis, 2) char combustion time and 3) maximum relative swelling give, for example, an estimate of how easy it is to direct the black liquor burning onto the [GLOSS]char bed[/GLOSS] due to its swelling characteristics. These characteristics are applicable for the lower and upper part of the furnace. A high swelling black liquor is more easily lifted with the upwards gas flows in the boiler than a low swelling black liquor and this can lead to a significant amount of black liquor being taken up to the upper furnace. These black liquor particles are called “[GLOSS]carryover[/GLOSS]”. Carryover particles can cause considerable [GLOSS]fouling[/GLOSS] of the heat surfaces. On the other hand, a high swelling black liquor has a higher internal surface and is therefore more reactive than the low swelling black liquor. This affects both the burning behavior of the char bed as well as how much combustible carbon reaches the char bed. For high swelling liquors more char can burn in flight instead of on the char bed. High swelling liquors give a porous and reactive char bed whereas low swelling liquors gives denser char bed.
The combustion times give, together with the swelling characteristics, indications of where in the furnace the combustion takes place, e.g. a highly swelling liquor with long char burning can be more easily carried over and be still burning in the upper part of the furnace, thereby shifting the heat load higher up.
The volatile carbon (volatile-C) and fixed carbon (fixed-C) provide estimates of how much carbon is released in the lower part of the furnace due to pyrolysis and how much carbon can be expected to remain in the char bed. These numbers are important for deciding how much air has to be fed to the char bed surface through the primary and secondary air-ports, and to the area above the bed for mixing and combusting the pyrolysis gases. The numbers also give indications of local heat load in the furnace.
The SO2 formation tendency tells how much sulfur is released from the black liquor in the lower part of the furnace during the pyrolysis stage. This gives an indication of the liquors tendency to cause SO2 emissions, however this is not the same as the recovery boiler SO2 emission number because sulfur readily reacts in the furnace with sodium vapors (fume) forming dust via condensation. Sodium release in the lower part of the furnace increases with temperature and therefore the SO2 emission is dependent on both the liquor specific SO2 formation tendency and the temperature in the lower furnace. The SO2 tendency can be used for calculating how much sodium needs to be volatilized to capture all formed SO2 as Na2SO4.
Finally, the NO formation tendency gives an estimate of the emission of NO from the recovery boiler if no specific NO reduction measures are taken. Recovery boiler NO emissions are mainly dependent on fuel nitrogen, air staging and liquor firing strategy. Temperatures in the recovery boiler are comparably low and thermal NO is not formed. Air staging is the primary measure available for decreasing the formation of NO from the volatile fuel nitrogen. An essential part, up to 30% of the fuel nitrogen can remain in the char after pyrolysis, finally forming cyanate in the [GLOSS]inorganic smelt[/GLOSS]. This cyanate reacts to form ammonia in the green and white liquors of the re-[GLOSS]causticising[/GLOSS] plant.
2. Experimental and definitions
Pyrolysis and char combustion time, and maximum relative swelling are measured at 800°C in an air atmosphere in a muffle furnace using single black liquor droplets of a size typical for a recovery boiler.
Single black liquor droplets are combusted in the muffle furnace and the event is recorded using a video camera. Droplets of around 10mg weight (~2.5mm in diameter) are first attached on a platinum hook using a spatula. The hook is hung at the end of a rod and lowered into the hot muffle furnace through an opening in the top of the furnace. The combustion of the droplet is recorded using a video camera and the video images are analyzed. The length of each combustion stage is determined and the physical swelling of the pyrolysed droplet is measured.
The pyrolysis stage (given in seconds) includes the decomposition of organic compounds and gas evolution. This results in the initiation of droplet swelling and/or a visual flame. The pyrolysis time is defined in the experiments as the time from first swelling or visual appearance of flames (whichever is first) to the time of maximum swollen volume or disappearance of flames (whichever is last).
In the char burning stage (also given in seconds) the char carbon is oxidised, leaving only the black liquor smelt remaining on the hook. The char burning time is defined as the time from maximum swollen volume or disappearance of flames (whichever is last) until the char carbon has been oxidized (this is visually noted as a clear residue collapse, forming a smelt bead on the hook).
The specific swollen volume during pyrolysis (Vsw in cm3/ g dry solids) is calculated by measuring from the video images the maximum height (h, in mm) and width (w, in mm) of the swollen droplet. The specific swollen volume (Vsw) is calculated with the formula:
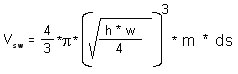
where, m= droplet weight (in mg) and ds is the dry solids of the black liquor in %. The volume is at maximum at the end of the pyrolysis stage.
The last four characteristics: volatile and fixed carbon, SO2 formation tendency and the NO formation tendency are measured by burning single black liquor droplets in a closed quartz glass reactor inside a muffle furnace at 900°C in an atmosphere of 10% O2 and 90% N2. Droplets of around 40mg weight (~3.5mm in diameter) are placed on a quartz glass cup with low edges. The sample holder is hung at the end of a rod and is in the experiment lowered into the reactor. The gas formation profiles during combustion is recorded using online gas analyzers (CO, CO2, NO and SO2).
The amount of volatilized carbon (volatile-C) can be determined from the CO2 concentration in the exhaust gas by assuming 100% conversion of all volatized carbon to CO and CO2. This assumption is reasonable given the relatively high oxygen concentration. This can be seen in Figure 2 as a high initial peak which is marked volatile-C. The volatile-C can be calculated by integrating the area under the curve. The figure shows results of four replicate samples. It is given as amount of carbon released per gram of dry sample (g C/ g dry solids).
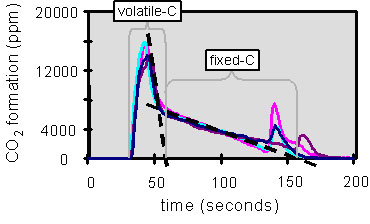
Figure 2. CO2 formation profile during combustion (900°C, 10% O2) of a 40mg BL droplet. Curve divided into pyrolysis carbon and fixed carbon.
The fixed carbon is the amount of carbon released during char burning and is marked in Figure 2 as fixed-C. It is calculated by integrating the area under the curve. It is given as amount of carbon released per gram of dry sample (g C/ g dry solids).
The NO formation tendency is measured from a similar curve (for NO) recorded with a chemiluminescence on-line NO analyzer. The NO is also divided into pyrolysis-NO and char burning NO. The NO formation tendency is calculated from the integrated amount of NO found under the curves. The amount is recalculated to recovery boiler NO emission using the calculated amount of flue gases formed from that specific black liquor. It is given as ppm NO at 3% O2 in dry flue gases.
The SO2 formation tendency is calculated in similar manner as the volatile-C and fixed-C, but by using the SO2 formation curve from an online NDIR SO2 analyzer connected to the experimental system. It is given as mg S / g dry solids.
3. Standard methods used on black liquors
Some pulping research laboratories perform a small number of standard measurements developed for other fuels to characterize black liquor. These can be considered to give some additional information about the combustion but they have some limitations when applied to black liquor combustion due to the unique nature of black liquor.
Ash content by DIN 51719 – The fuel sample is burned two hours at 815 °C (± 15 °C), cooled down and weighed thereafter. The ash content results from the weight difference before and after the burning.
Difficulties: The method does not cover the weight loss starting at around 800°C due to the reaction of Na2CO3 with char carbon resulting in a production and volatilization of CO, CO2 and Na. The method can be used as a guideline for the amount of smelt.
Volatile constituents by DIN 51720 – The fuel is carbonized seven minutes at 900 °C (± 10 °C). The heating is realized without air exchange in a crucible with a cover. The decrease in weight (less water content) corresponds to the proportion of the volatile constituents.
Difficulties: The method includes the weight loss due to the above reaction of Na2CO3.
Sources
[1] FORSSÉN, M., HUPA, M. AND HELLSTRÖM, P. (1999): “Liquor-to-liquor differences in combustion and gasification processes: Nitrogen oxide formation tendency”, Tappi J., 82:3, 221-227.
[2]HUPA, M.. SOLIN. P. and HYÖTY. R, “Combustion Behaviour of Black Liquor Droplets’, J. Pulp Paper Sci. 13(2) :J67-J72 (1987).
[3] NOOPILA, T.. ALEN, R. and HUPA, M., “Combustion Properties of Laboratory-Made Black Liquors”, J. Pulp Paper Sci. 17(4): J105-J109 (1991).
[4] WHITTY, K., BACKMAN, R., FORSSÉN, M., HUPA, M., RAINIO, J., AND SORVARI, V., “Liquor-to-Liquor Differences in Combustion and Gasification Processes: Pyrolysis Behavior and Char Reactivity”, J. Pulp Paper Sci., 23:3, J119-J128, (1997)