-
How do I analyse coal ash chemistry?
Date posted:
-
-
Post Author
dev@edge.studio
1. Background
This Combustion File (CF) stems from CF38 What is coal ash? The reader is also referred to CF177 for an introduction to [GLOSS]coal[/GLOSS].
2. Main Analysis Methods
The standard methods for determination of the content of inorganics in coal are chemical analyses after ashing or gravity fractionation as described below.
Recently, more advanced methods have become available. These include for instance chemical fractionation analysis ([GLOSS]CFA[/GLOSS]) and scanning electron microscopy ([GLOSS]SEM[/GLOSS]) combined with energy dispersive X-ray analysis ([GLOSS]EDX[/GLOSS]).
The new methods both provide more information about the abundance, size and association of inorganic components in the coal.
Unfortunately, these are seldom used as standard coal analysis (See CFs 24, 48 and 120), which usually only contain the [GLOSS]proximate analysis[/GLOSS] and [GLOSS]ultimate analysis[/GLOSS] of the coal.
In the proximate analysis, the total moisture, air-dried moisture (inherent), volatile matter, ash and fixed carbon content of the coal are given. In the ultimate analysis, the elemental composition of the organic matrix of the coal is given, which includes the carbon, hydrogen, nitrogen, sulphur and oxygen (by difference) content of the coal.
High temperature ashing ([GLOSS]HTA[/GLOSS]) is the normal standard method (ASTM Standards D 3174) for concentration of the inorganic constituents in coal before chemical or other analysis. It consists of the oxidation of a pulverised coal sample at 1023K (750°C), and is followed by a chemical analysis of the ash produced by the oxidation.
The limitations of this method include the transformations and reactions that occur in the inorganic constituents during the ashing procedure, the mass loss (water loss, CO2 from carbonates, and sulphur from pyrites) from the inorganics taking place during the ashing procedure, an absorption of H2O, CO2 and SO2 by the organically associated alkali and alkaline earth metals, and the fact that no information about the association and abundance of the inorganic species result from the method [Benson et al., 1993].
Low Temperature Ashing ([GLOSS]LTA[/GLOSS]) is a method to concentrate the inorganic species before analyses. LTA is an ashing procedure for a sample of pulverised coal at approximately 480 K in an oxygen plasma atmosphere. The oxygen present gradually breaks down the organic material in the coal, without causing (excessive) thermal decomposition of the inorganic species.
The method works well for high ranked coals, but demands (very) long ashing times for the lower rank coals with higher amounts of organically associated cations. The reason for this could possibly be that the organically associated species are not contained in the resulting ash, or that they are transformed during ashing.
The technique is better than HTA as it leaves an almost unaltered sample of the inorganic species present in the coal, especially for high rank coals. However, the technique still transforms some of the inorganics present, for instance for organically bound calcium, sodium, magnesium and iron.
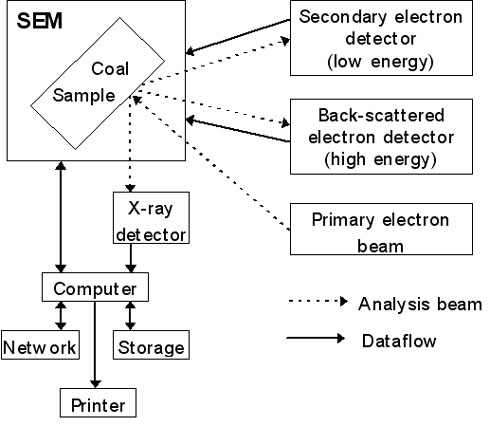
Figure 1: Typical configuration of SEM apparatus.
In the scanning electron microscope, a sample is examined using an electron beam as the source of light. The typical configuration for a SEM is given in Figure 1.
The two signal types most commonly used for production of pictures are Secondary Electrons ([GLOSS]SE[/GLOSS], emitted from the sample with an energy lower than 50 eV) and Back Scattered Electrons ([GLOSS]BSE[/GLOSS], emitted from the sample with and energy higher than 50 eV).
Energy Dispersive X-ray (EDX) detection is generally used for chemical analysis. The origin of the secondary and back-scattered electrons is illustrated in Figure 1.
The image produced by secondary electrons is a light/shadow image that reflects the surface of the sample. In BSE images, the intensity of the back scattered electrons are a function of the atomic number; the higher number, the brighter it appears.
The Computer Controlled SEM ([GLOSS]CCSEM[/GLOSS]) technique makes it possible to evaluate the size, shape (deviation from circularity), quantity, and (semi) quantitative composition of mineral grains in coal, due to the combination of CCSEM, backscatter electron (BSE) imaging and energy dispersive X-ray (EDX) detection.
The coal particles to be analysed are mounted in an epoxy or wax matrix, and the analysis is carried out at a polished cross section of the coal-mounting plug. Composition determinations can only be performed for mineral grains larger than 1 mm (2 mm in practice), due to limitations in electron beam size.
It is possible to distinguish the mineral particles in the BSE image, as they appear brighter than the organic coal matrix and the mounting media. When performing a CCSEM analysis, the electron beam is programmed to scan over the field currently in view, and locate the bright inclusions corresponding to mineral grains or other ash species. Hereafter the beam performs 8 measurements of the diameter of the inclusion, thereby locating its centre.
In the centre of the inclusion, an energy dispersive spectrum ([GLOSS]EDS[/GLOSS]) is collected for two seconds. The system is commonly set to analyse for the following 12 elements: Na, Al, Si, P, S, Cl, K, Ca, Fe, Mg, Ba and Ti. However, these settings are individual to the apparatus in use, and/or the person using the apparatus.
The EDS of a mineral grain gives the elemental composition of the grain. Using this information, the mineral composition of the grain can be found. This is done via a classification system, based on the compositions of minerals, as well as data regarding mineral chemistry. Also mineral associations (a discrete particle containing at least two adjacent or intimately associated minerals) are identified in this way.
The particle diameter is determined by the insertion of several horizontal and vertical cords over the particle, until the centres of the two types coincide. This point is taken to be the centre of the particle. A set of cords (up to 16) at equally spaced angles is then constructed through the centre, and the average length of these is taken as the diameter of the particle. An alternative is to determine the SEM-based particle size as the diameter of a circle with the same area as the particle.
The measurements of particle size are in general moved artificially towards the smaller particle sizes, because the measurements have been performed on cross sections of the mineral particles. This way, a spherical particle can have any diameter between zero and the real diameter.
For low-rank fuels, the quantification, abundance and type of inorganic elements can be analysed by chemical fractionation. In chemical fractionation analysis, the inorganic constituents are selectively extracted from the coal by successive leaching steps with different materials. The principle of the method is shown on Figure 2.
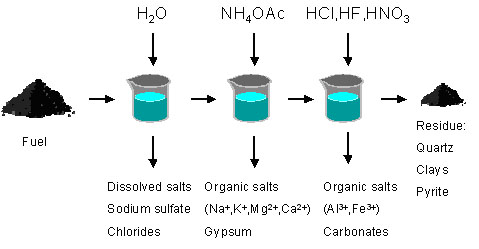
Figure 2: The principle of chemical fractionation analysis.
If also trace metals are to be collected, the chemical fractionation is continued with two more acids; HNO3 and HF.
This is a very useful analysis with regard to the deposition propensities of a certain coal, but provides the most information for low rank coals and other low rank fuels. Chemical fractionation can for instance be used to distinguish active and inactive alkali in coal and other fuels. Alkali, soluble in a weak acetic acid solution or water, can be considered active alkali species, which will probably vaporise and/or react or condense during combustion. Inactive alkali will remain as clays and shales during combustion.
3. Other Analysis Methods
Several other techniques are used to identify inorganic species in coal. These include for instance X-Ray Diffraction ([GLOSS]XRD[/GLOSS]) for determination of crystalline mineral phases, X-ray Absorption Fine Structure analysis ([GLOSS]XAFS[/GLOSS]) to determine valence state and chemical form of many elements, Mössbauer spectroscopy for determination of iron forms present, Transmission Electron Microscopy ([GLOSS]TEM[/GLOSS]) for characterisation of submicron grains or particles, Infra Red ([GLOSS]IR[/GLOSS]) spectroscopy, Thermo Gravimetric Analysis ([GLOSS]TGA[/GLOSS]), Atomic Absorption Spectrometry ([GLOSS]AAS[/GLOSS]), and Differential Thermal Analysis ([GLOSS]DTA[/GLOSS]).
Of these, XRD and IR spectroscopy demand low temperature ashing, which can be very time consuming.
Acknowledgements
CHEC is co-funded by ELSAM, ENERGY E2, the Danish Technical Research Council, the Danish and Nordic Energy Research Programmes, and the European Union.
Sources
[1]Benson, S.A., Jones, M.L. and Harb, J.N., 1993, Ash formation and deposition. In Smoot, L.D. (Ed), Fundamentals of Coal Combustion – for Clean and Efficient Use, Coal Science and Technology 20, Elsevier Science Publishers, Amsterdam, ISBN 0-444-89643-0, Chapter 4, pp. 299-373
[2] Bryers, R.W., 1996, Fireside slagging, fouling and high temperature corrosion of heat-transfer surface due to impurities in steam-raising fuels, Prog. Energy Combust. Science, 22 (1), pp. 29-120
[3]Laursen, K, 1997, Characterization of Minerals in coal and Interpretations of Ash Formation and Deposition in Pulverized Coal Fired Boilers, Ph.D. Thesis, volume 1 and 2, Geological Survey of Denmark and Greenland, Ministry of Environment and Energy, ISBN 87-7871-022-7
[4] American Standard Testing Methods (ASTM) – D3174-02 Standard Test Method for Ash in the Analysis Sample of Coal and Coke from Coal, 2002, ASTM International, West Conshohocken, PA, USA.