-
Digital Twin Technology for Biomass Combustion
Date posted:
-
-
-
Post Author
Bernhard PetersProfessor of Thermo-/Fluiddynamics, University of Luxembourg
-
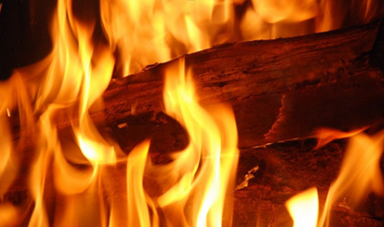
-
Generating heat through burning of wood and other biomass is most probably the oldest energy technology applied by man. Nowadays, commercial combustion is a well-established technology in both industrialised and developing countries. While carbon neutrality, reduction of greenhouse gases and decentralised availability make biomass a very attractive fuel, a variety of fuel properties and associated emissions during non-optimal thermal conversion constitute major challenges for design and operation of furnaces. Furthermore, today’s markets are exposed to fierce competition and require products that go beyond better quality at shorter innovation cycles. In addition, physical prototyping is rarely compatible with innovative product development, cost and time constraints. Therefore, application of numerical models to predict the behaviour of physical systems is common use in engineering and related disciplines.
Illustration 1: 3D view of the cut combustion stations or in a cloud without investing into a highchamber (top) and a slice (bottom) showing performing computing environment. Thus, it covers theparticle pyrolysis progress and streaks of large range from small domestic stoves (1 to 10 kW) as formed tar
Recently, the rapid development of algorithms, data and computers created the novel and innovative digital twin technology. In this prospective, a digital twin is regarded as a virtual replication of the physical process from which it is almost indistinguishable in its final stage. In particular, a simulation-based digital twin (SBDT) includes first principle models from physics, chemistry or engineering such as computational fluid dynamics (CFD) as a widespread application. Similarly, the XDEM software, based on the Extended Discrete Element Method, is an advanced and innovative simulation environment from which simulation-based digital twins for a wide field of applications in the processing industry such as biomass combustion may be created and is depicted above.
XDEM considers the granular material e.g. biomass or pellets as discrete entities for which internal temperature, species and reaction progress are estimated. The particles are coupled to the gas phase via heat, mass and momentum transfer that all together replicates the entire system. Furthermore, XDEM is a computationally high performing tool that achieves an unprecedented scalability for parallel performance with the novel co-located partitioning technique developed at the University of Luxembourg. It enables users to run digital twins on moderately sized work to large boilers (150 to over 1 MW).
For this purpose, XDEM has excellent features to address this challenge as follows:
- extended material property data base
- validated reaction schemes for drying, pyrolysis, gasification, combustion and emissions
- sophisticated interaction models and shapes to describe motion of biomass particles
- exchange of mass, energy and momentum e.g. drag between solid particles and gas flow
- computational grid independent of particle size allowing a sufficient resolution of the reacting flow
- advanced high performance concepts for both standard and high performance computers achieving unprecedented performance
In addition, XDEM software comes with extended documentation including numerous tutorials. Commercial licences, training and professional consultancy covering all aspects of software development and maintenance are offered by Wikki GmbH.
Illustration 2: Pellet combustion in a domestic stove
Hence, employing the proposed digital twin technology with XDEM immediately offers detailed results for both, the particulate and gas phase. Furthermore, digital twins allow avoiding a constraint on physical prototypes namely to isolate and observe the effect of an individual parameter while all others being constant (ceteris paribus). Thus, a large number of hypotheses on causal relationships may be evaluated individually that simply do not exist with physical prototyping. Thereby, phenomena are observed that were hidden before. Results obtained from digital twins expand the knowledge base and unveil new relations between components of an application and its underlying physics. Hence, a digital twin is regarded to be the first step in a chain for innovative and advanced processes in engineering and thus, determines significantly the quality of the end product and success of your company.
Contacts:
Bernhard Peters
Professor of Thermo-/Fluiddynamics, University of Luxembourg
Email: bernhard.peters@uni.lu
Website: luxdem.uni.luHenrik Rusche
CEO, Wikki GmbH
Email: henrik.rusche@wikki-gmbh.de
Website: www.wikki-gmbh.de