-
How do I measure pulverised coal char combustion in oxy-fuel atmosphere using IPFR/DTF?
Date posted:
-
-
Post Author
dev@edge.studio
1. Background
The concept of pulverised fuel characterisation, together with the isothermal plug flow reactor (IPFR) or drop tube furnace (DTF) has been explained in CF48. The main applications of the IPFR or DTF are the studies of [GLOSS]volatile matter[/GLOSS] release, [GLOSS]char[/GLOSS] residue combustion, fuel nitrogen fate and ash formation processes. The biggest advantage of this technique is that it reproduces operational conditions relevant to industrial pulverised fuel combustion process – reaction temperatures up to 1773 K, particles’ heating rate and residence time up to 105 K/s and 3 seconds respectively.
The main characteristics of the IPFR/DTF are:
– vertical (most often ceramic) reaction tube
– electrically heated walls
– laminar or transient flow
– movable feeding and sampling probes
– almost instantaneous quenching (stoppage) of the reaction.
More details about the IPFR are given in CF135. The description of the procedure of measuring the char combustion under standard (air-fired) conditions are introduced in CF184.
This combustion file concentrates on the coal char combustion methodology under oxy-fuel conditions.
2. Char burnout measurements in the oxy-fuel conditions
Char preparation
In order to conduct char combustion tests it is necessary to prepare the char sample in conditions relevant to industrial scale ones, i.e. it is necessary to ensure that the particle heating rate and reaction temperature are at least 104 K/s and 1273 K respectively.
In [GLOSS]oxy-coal[/GLOSS]/[GLOSS]RFG[/GLOSS] combustion, raw coal is devolatilised in a gaseous atmosphere consisting of almost pure carbon dioxide (at least 90%vol.).
The residence time of the particles should be selected carefully – it should be long enough to ensure complete devolatilisation but simultaneously short enough to hinder undesired effects, such as thermal annealing and gasification with CO2.
Good practice is to produce at the beginning a small amount of char and immediately perform its [GLOSS]proximate analysis[/GLOSS] in order to assess the extent of the devolatilisation and/or gasification. After ensuring that the char meets the above-mentioned requirements, the production of greater amounts can be performed.
Char combustion
Char combustion trials in the IPFR/DTF should be conducted in various gas atmosphere compositions – O2/N2, N2/CO2, N2/H2O in order to determine the rates of the individual reactions and their influence on the overall combustion rate. Additionally, runs with the combination of all particular species present in the combustion system – O2/CO2/H2O are recommended. Although simple comparison between air and oxy-fuel conditions (burnout level) can be performed in just O2/N2 and O2/CO2 atmospheres, the determination of the [GLOSS]kinetic parameters[/GLOSS] is more complicated.
One should pay attention to the combustion regime the reactor operates in and take this into account when determining suitable model parameters. Three regimes are defined:
· Regime 1: when the combustion rate is kinetically (via chemical reactions) controlled (at low temperatures or small particle sizes).
· Regime 2: when the combustion rate is controlled both by chemical reactions and mass transfer (at high temperatures and small particles – this is the range where most IPFR/DTF reactors operate).
· Regime 3: when the combustion rate is only controlled by mass transfer (at high temperatures or large particles).
It is recommended that char oxidation tests be performed in at least three temperatures and three concentrations of the given species in order to determine the influence of the temperature and reaction order. In case of the O2/N2 and O2/CO2 experiments it is suggested to conduct the experiments at the following temperatures and O2 concentrations (N2 and CO2 are diluents): 1173, 1373, 1573 K at 6 vol.% O2 and additionally at 1573K with 2 and 4 vol.% O2.
Char produced as mentioned above is injected into the IPFR /DTF such that different residence times at each condition are obtained. The solid reaction products are instantaneously quenched with pure nitrogen to stop further reaction and sampled in a cyclone system. Collected samples are used for further analyses.
Determination of the char burnout
Char conversion levels (burnout) are determined using the change in combustible fraction of the particle:

where: CF, 0, 1 denote combustible fraction, initial char and sampled char (after set residence time) respectively.
Assuming that the mass of the [GLOSS]mineral matter[/GLOSS] in char doesn’t change during experiments, one can write:

Combining eq. 2 into 1 one receives relation based on the ash tracer:
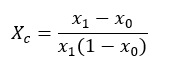
So, in order to determine the char burnout it is only necessary to determine the ash content of the initial and sampled char.
One should note that eq. 2 is usually valid for anthracites and bituminous coals. In the case of the lignite coals (or biomass) their mineral matter can decompose during the combustion, it is recommended to check the ash composition of the initial coal and its char. When the ash composition changes during experiment one should either adjust the operating conditions (temperature) or choose a different tracer (e.g. titanium).
3. Conclusion
Data obtained in the IPFR/DTF during char combustion in oxy-fuel combustion includes information about the conversion levels in conditions comparable to full-scale boilers and can be used to predict combustion in oxy-fuel conditions using [GLOSS]CFD[/GLOSS] code.
The data collected under oxy fuel conditions can be viewed on the RELCOM website (www.relcomeu.com) and within the IFRF’s Solid Fuel Database http://sfdb.ifrf.net.
Acknowledgements
The research leading to these results has received funding from the European Community’s Seventh Framework Programme (FP7/2007-2013) under grant agreement n° 268191.