-
What are the alumina manufacturing processes?
Date posted:
-
-
Post Author
dev@edge.studio
1. Introduction
The complete range of processes undertaken in the minerals processing industry was outlined in CF 255. This combustion file gives more specific detail of the processes in use for the manufacture of alumina.
2. Alumina
The primary material for the production of aluminium is alumina, Al2O3, which is smelted electrically in an arc furnace. Alumina is also used as an abrasive, refractory, and as a catalyst substrate. Alumina is produced from naturally occurring Bauxite (~50% hydrated alumina) via the Bayer process. The final stage of this process requires the refined hydrated alumina, Al2O3.3H2O, to be calcined at ~1100oC to remove the bound water. Figure 1 shows the breakdown of bauxite production (as processed alumina) by principal countries. The processing of the bauxite to alumina is carried out at a relatively few large refinery operations that are not always situated in the source country. Refinery operations are usually co-owned by the major aluminium companies, and are situated in Australia, USA, Canada, West Indies, Brazil, Guinea, China, USSR, India, France, Greece, Italy, Ireland, UK, Spain, Germany.
There are two types of process furnace in which the calcination of alumina trihydrate is carried out, either a long rotary kiln or a [GLOSS]flash calciner[/GLOSS] or[GLOSS]fluid bed calciner[/GLOSS]. World production was fairly evenly divided between these two competing technologies, but new installations are exclusively flash or fluid bed calciners and several [GLOSS]rotary kiln[/GLOSS]s are currently (2003) being replaced by the newer technology. The material is fed in both systems to the furnace as a damp (~5% moisture), finely divided powder of ~130mm mean diameter, where it is heated to between 800oC and 1000oC to detach the water of crystallisation. The resulting alumina is produced in various crystalline phase forms (a,q,c,g,d) depending on the time/temperature history of the particle after initial [GLOSS]calcination[/GLOSS].
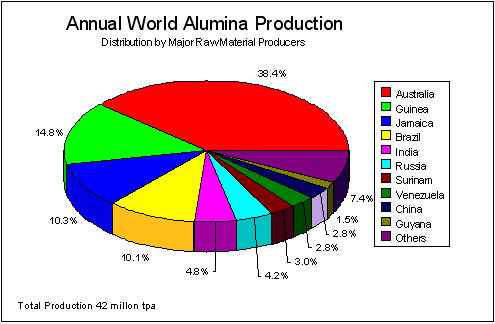
Figure 1 World Production of Alumina in 1993 (European Minerals Yearbook / Industrial Minerals Handy Book)
The rotary alumina kiln is fitted with a dust return system, as partly processed material is entrained into the combustion products in the kiln and coolers, and collected by a cyclone/precipitator system for subsequent recycle. Material cooling is usually carried out in two stages; a primary [GLOSS]planetary cooler[/GLOSS] or [GLOSS]rotary cooler[/GLOSS], followed by a [GLOSS]fluid bed cooler[/GLOSS]. Typical specific fuel consumptions for a standard rotary kiln is in the range of 4.5 – 4.2 MJ/kg, although rotary kilns fitted with intermediate burners approximately half way along the kiln can achieve 3.8 – 3.6 MJ/kg.
Lime in the alumina industry
Low grade bauxite typically contains ~40% and ~12% of silica, and [GLOSS]limestone[/GLOSS] is used to convert this into insoluble silicate at an early stage in the combination Sainte Claire Deville-Bayer process, allowing the alumina to be extracted as soluble aluminate.
The bauxite is finely ground with Na2CO3 and CaCO3 and sintered in a rotary kiln at 1100oC to calcine the sodium carbonate to sodium oxide and the limestone to [GLOSS]quicklime[/GLOSS]. The sodium oxide reacts with the alumina to form sodium aluminate (NaAlO2), and the quicklime reacts with the silica to produce dicalcium silicate (Ca2SiO4). The sodium carbonate is recovered from the sodium aluminate solution by reaction with CO2, which precipitates Al(OH)3.
[GLOSS]Lime[/GLOSS] is also produced in rotary kilns in an alumina refinery to re-causticize the sodium hydroxide used in the primary bauxite digestion process in a similar manner to the pulp and paper industry.
Sources
[1] European Minerals Yearbook
[2] Industrial Minerals Handy Book