-
How is a flameless combustion system started up from a cold state?
Date posted:
-
-
Post Author
dev@edge.studio
1. Background – flameless firing
Controlled and stable firing can be carried out without a burner-stabilized, conventional flame under suitable circumstances: as a basic condition, reactants must be pre-heated in the combustion chamber above their [GLOSS]self-ignition temperature[/GLOSS], before combustion takes place. This technique, referred to as [GLOSS]flameless combustion[/GLOSS] (CF171), is confined to high temperature processes (above the temperature threshold mentioned above); it is often, but not necessarily, associated with high preheat of the combustion air.
Many practical systems may fulfil the above condition at regime, but fail to do so at start-up from cold plant: then some device (usually a conventionally stabilised flame system) must be provided to preheat the plant above threshold.
2. How do I ensure safe operation starting from cold?
Figure 1 qualitatively describes the behaviour of a mixture of natural gas and air in a temperature vs concentration diagram at atmospheric pressure: the lower and upper [GLOSS]flammability limits[/GLOSS]define the range wherein a flame is possible (but an explosion as well!): fuel-rich or fuel-lean mixtures outside this range will not burn/explode. This information can be found for many fuel gases in charts prepared by safety officers in mines, but is available at room temperature only.
By increasing temperature, the flammability range gets wider and wider. It loses meaning eventually, when self-ignition temperature is approached or exceeded; this implies two consequences:
– combustion occurs anyway, irrespective of air to fuel proportions as long as there is enough oxygen and fuel available
– no explosions are to be expected
The latter item is relevant for safety purposes: tests on a large experimental furnace have shown that igniting in flameless combustion mode is quite smooth as long as the temperature is well above threshold, while ignition exhibits visible discontinuity effects (pressure jump, noise etc.. ) when temperature is reduced close to or just below self-ignition threshold.
The self-ignition temperature is a function of pressure (» decreases with increasing pressure) and of fuel/oxygen/inert concentration. It is strongly affected by the chemical ignition scheme of the particular fuel molecule: for example, self-ignition can be as low as » 215 °C for heptane (C7H16), while it is much higher for the much smaller CH4 molecule (» 630 °C, [3]). H2 is somewhat in between (» 400 °C) and pure CO is hard to burn even at high temperature and fuel mixtures are even more difficult to predict.
Figure 1: Flammability limits of natural gas air mixtures
In industrial practice, a variety of fuels can be used and as a consequence, a temperature limit high enough for safe thermal ignition in all conditions should be envisaged. Under particular, controlled conditions this limit might be adapted to the particular circumstances, but for general purposes a safety temperature threshold = 750 °C is considered in safety prescriptions concerning furnaces [2]; furnaces and processes permanently above this threshold, are even allowed to avoid [GLOSS]flame detector[/GLOSS]s and safety shut-off valves.
Flameless combustion is not safe or possible below threshold: then it is necessary to use a conventional flame-stabilized system from cold start-up to temperature above 750 °C. In control of industrial furnaces, the threshold furnace temperature for flame to flameless transition is usually set to » 850 °C for safety; only then is switch over from flame to flameless firing allowed. When temperature goes down instead, a hysteresis is applied and transition flameless to flame occurs at » 800 °C.
3. What are possible design solutions for start-up from cold?
There are as many devices to inject air and fuel through the burner in order to carry out flameless combustion, as there are combinations of air and fuel nozzles to generate a conventional flame-front stabilised flame (CF173, CF215). Generally, the air flow pattern is most critical in burner design because air flow is » 5 – 10 times larger than gas flow: therefore gas injection nozzles are comparatively small and can easily accommodate twofold injection, that is a primary gas for flame firing and a secondary gas for flameless firing.
The cold furnace is started with flame firing and as soon as the furnace temperature increases above safety threshold (» 850 °C), flameless firing can be switched on automatically to take advantage of flameless firing, e.g. low NOx emissions, high temperature uniformity, etc. (CF171, CF172).
A basic difference between stable flame and flameless combustion is that in the former a local, stationary, high intensity ignition source must be provided whereas this is not required in the latter case. In flameless combustion, a rather distributed combustion pattern is controlled by gradual entrainment of hot flue gases; these pre-heat the mixture of combustion air and fuel above the self-ignition temperature and at the same time prevent high flame temperature because of the ballast of inert components.
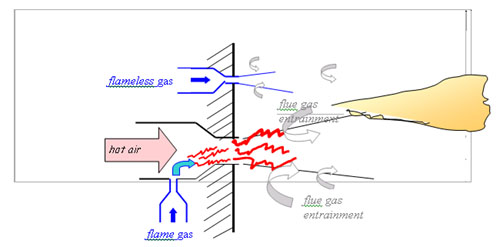
Figure 2 – Schematic of two-gas injection
Figure 2 shows a conceptual scheme, by way of example only: in many cases, air is preheated and cross injection of fuel gas easily produces a flame front (red broken). Gas injection far from combustion air (flameless port) produces flameless combustion.
There are two potential start-up approaches:
– gradual transition from flame firing (fuel: 100% from flame gas ports) to flameless combustion (fuel: 100% from flameless gas ports); supplying a fraction of fuel to both nozzles, part of the fuel may generate a stable and lean flame, while the rest of the fuel will burn downstream far away from the burner near-field
– a well defined step between the two modes; in general this implies flame mode up to » 850 °C and flameless mode above, with an hysteresis of some 20-50 °C when the furnace falls lower than » 800 °C
In furnace technology, the second approach is usually better from the point of view of safety. However, the choice depends on the peculiar application, taking into account that flameless is not only applicable to furnaces, in particular for reheating and heat treatment, but also to other devices (e.g. gas turbines).
Sources
[1] J. A. Wünning and J. G. Wünning – Flameless oxidation to reduce thermal NO-formation – Progress in Energy and Combustion Science, 23, 1997, #1, 81-94
[2] EN 746-2 Industrial thermo-processing equipment: safety requirements for combustion and fuel handling systems
[3] N.V. Nederlandse Gasunie, Properties of natural gases, 1988.