-
How do I prevent fluidised bed agglomeration?
Date posted:
-
-
Post Author
dev@edge.studio
1. Bed agglomeration
[GLOSS]Bed agglomeration[/GLOSS] problems in fluidised-bed conversion ([GLOSS]fluidised bed combustor[/GLOSS] or gasification) are related to a high content of alkali metals (K, Na) in the fuel. Combined with high content of sulphur (in combustion), chlorine, silica and phosphorus, low-melting compounds or [GLOSS]eutectic[/GLOSS]s are formed, which become deposited on the bed particles, coating them with a sticky [GLOSS]ash[/GLOSS] layer acting as to glue particles together.
Bed agglomeration in fluidised-bed conversion of [GLOSS]biomass[/GLOSS] is related to a high content of potassium, which concentrates in regions of most vigorous growth. Likely problematic fuels are: residues of agricultural crops, young [GLOSS]energy crops[/GLOSS] or other biomass containing young organic material.
A detailed description is given in CF 50 – What is bed agglomeration.
2. Prevention of agglomeration
The prevention of bed-agglomeration is mainly threefold:
a) Avoiding the combinations of fuels having elements responsible for agglomeration,
b) Removing problematic elements from the fuel and,
c) Avoiding operational conditions advantageous for agglomeration.
Growing and harvesting
1) Using fertilising with low content of chlorine.
2) Reducing the share of young biomass because of their high K content.
3) Avoiding contamination with soil particles to reduce the silica content by careful harvesting.
4) Allowing weathering to leach K and Cl; afterwards drying of the fuel is required – See Figure 1 below
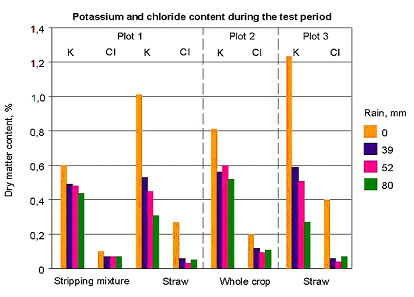
Figure 1: The leaching of potassium and chloride
according to the amount of rain accumulated.
(Created by Niels Peder Madsen, Danish Institute of Agricultural Sciences)
Fuel pre-treatment
1) Removing non-fuel components, which may concentrate at the bottom of the bed locking the mass and heat transport.
2) Degrading oversize fuel materials. Under slow reaction conditions, coarse char particles may accumulate destabilising the fluidisation.
3) Separating the soil (mainly silica) attached to the fuel by washing, sieving or fluid dynamic separation.
4) Washing out alkaline and chlorine in hot water.
5) Decreasing the fluctuation in fuel quality by homogenisation.
Blending
1) Blending biomass with coal and wood: alkaline from biomass may be bound into high melting aluminium silicates of coal.
2) Avoiding combinations of fuels which may lead to agglomeration such as
a. high alkaline and high chlorine fuels
b. biomass rich in KCl (e.g. straw) and high sulphur coal
c. high alkaline biomass and high silicate coal/biomass.
Fluid dynamic control
1) Choosing proper gas velocity with given particle size.
2) Securing good air distribution at all loads.
3) High fluidisation velocity lowering the tendency of agglomeration and [GLOSS]deposition[/GLOSS].
4) Temporary increase of the fluidisation velocity to disintegrate the agglomerates. However, the increased velocity may decrease the bulk density of the fluidised area adjacent to the strong agglomerates settled to the bottom of the bed. Also, the temperature may rise during sudden velocity increase.
Bed particle management
1) Selecting bed material in according to the fuel type, additives and operation parameters to avoid [GLOSS]sintering[/GLOSS]; bed materials other than silica sand: hermatite (Fe2O3) found not to agglomerate at all, corundum (Al2O3).
2) Removing oversize material from the bed, originated from the insufficient fuel preparation or agglomeration.
3) Periodical refreshment of the bed inventory before the critical alkali concentration or critical agglomeration level is reached.
4) Limiting the retention of small particles, which may enhance sintering and agglomeration.
5) Chemical additives to reduce or delay the bed-agglomeration and defluidisation in combustion and gasification. Such additives are:
a. clay minerals (aluminosilicates), like kaolin (Al2SiO5(OH)4)
b. periclase (MgO)
c. calcite (CaO)
d. dolomite (CaCO3.MgCO3), limestone (CaCO3)
e. gibbsite (Al(OH)3).
The mechanisms and the corresponding additives are:
a. increasing the ash melting temperature; using periclase, calcite, clay minerals,
b. chemical [GLOSS]absorption[/GLOSS] of volatile alkali metals into stable high melting minerals; using kaolin,
c. influencing the viscosity of melted compounds; by using periclase,
d. removing sulphur before it reacts with the ash to form low melting compounds; using dolomite and limestone.
Other suspected mechanisms:
a. physical absorption of melted phases within porosity of added particles; using gibbsite,
b. powdering that makes melted phases act less sticky to the surfaces of other particles; using coal fly ash.
Temperature control
In general, the agglomeration is caused by melted ash or ash derived components acting as to glue particles together. Agglomeration can be avoided by keeping the temperature at a sufficiently low level allowed by the combustion /gasification process (unacceptable carbon losses, low reaction rate, emission formation) by:
1) Avoiding temperature excursions during start-up and shut down. Overfeeding fuel when reaching the setpoint temperature (i.e. due to incorrect operation) may result in large amount of char. This char starts to react at a fast rate around setpoint temperature, causing temperature overshoot. Similar event happens when changing to less reactive fuel.
2) Local temperature peaks should be avoided: improving distribution of fuel and oxygen; moderating the temperature near gas nozzles by adding steam to gasifiers or recirculating flue gas to combustor; better mixing in critical bed area (“golf steaming”); allowing higher particle flux through the freeboard or other critical parts;
3) Avoiding high concentration of oxygen in areas with high concentrations of char – since the temperature of burning char particles may be considerably higher than bed mean temperature – by improving the distribution of combustion air or gasification agent.
In contrast, choosing sufficiently high temperature may help to avoid agglomeration. The alkali’s evaporated may condense at lower temperatures downstream and during temperature increasing some of the alkali’s may recombine into other sticky components with lower vapour pressure.
Acknowledgements
Acknowledgement to Mr. Bram van der Drift, ECN Biomass, for his help in literature research.
Sources
[1] A. van der Drift and A. Olsen: Conversion of biomass, Prediction and Solution Methods for Ash Agglomeration and Related Problems. Final Report, Non-Nuclear Energy Programme Joule 3 by European Commission, contract JOR3-95-0079.
Further sources to be added before publication