-
What data is available on the emissivity of firebrick and refractories as a function of temperature?
Date posted:
-
-
-
Post Author
Neil Fricker
-
1. Background
This Combustion File consists of a compilation of experimental data from a variety of sources on the [GLOSS]emissivity[/GLOSS] of refractories, glasses and coatings used in high temperature applications. The data is cast in the form of temperature dependent correlation equations that can be used for modelling purposes. Correlations for other materials may be found in four other linked Combustion Files:
· CF147 – metals
· CF149 – carbons and coal ash
· CF223 – glasses and ceramics
· CF224 – coatings, paints, paper, porcelain and water
Background information on the definition and general aspects of the surface emissivity of materials may be found in CF146. Information on the effects of surface roughness is presented in CF 150.
Users of this combustion file should note:
- The data are tabulated in HTML form lower on this page.
- The same data, prepared for calculation, are presented in individual Microsoft Excel Worksheets, all contained within a Workbook.
- The Excel Worksheets also contains two columns allowing the user to calculate surface emissivity directly by inputting a temperature value
- This workbook can be down-loaded by the reader and saved to a local hard disk.
- To achieve this click on the “xls” icon on the left hand side of the banner above. The file will be retrieved from the server, and with up-to-date versions of the browser, will appear in a separate window, from which it may be saved to the user’s hard disk.
- With the exception of the temperature input cells for the calculator, the data in these worksheets are protected – thus the reader cannot change the worksheet without knowledge of the protection password.
- However the reader can copy and paste the data into his/her own project work book as required – at this point the accuracy and integrity of the data becomes the responsibility of the reader.
- To overview the data available – see text and tables below.
- All credits and sources, and where necessary, instructions/advice for data use, are presented in this html file. These are not necessarily reproduced in the Excel Work Sheets.
2. The correlation equation
Section 3 lists the emissivity, e0(T), of a range of refractories as a function of temperature. These are expressed as least squares polynomials fitted to data from the references listed under Sources below. They are correlated by the expression:
e0(T) = a +10-5bT + 10-8cT2 +10-10dT3 (1)
where T is the absolute temperature (K)
and a, b, c, d are fitted coefficients.
Omitted entries for the coefficients should be taken as zero. Extrapolation beyond the quoted temperature range should be undertaken with caution especially for strongly non-linear relationships where the c and d coefficients are non-zero. The s.d. column contains the standard deviation of the individual emissivity measurements about the fitted line, but this is only included where a reasonable estimate is obtainable.
3. Emissivity data and correlation coefficients
The correlation coefficients to be used in equation 1 are shown in the tables below. For certain materials, a graphical representation of the emissivity against temperature replaces the correlations. This is shown in Figure 1.
Material |
e0(T) |
T range K |
Ref. |
e range |
||||
a |
b |
c |
d |
s.d. |
||||
Fire brick (Al/Si/Fe/O) |
|
|
|
|
|
|
|
|
low Al2O3 content |
0.9 |
-10 |
|
|
|
673 – 1673 |
5 |
0.83-0.73 |
medium Al2O3 content |
0.84 |
-20 |
|
|
|
673 – 1673 |
5 |
0.71-0.51 |
high Al2O3 content |
0.8 |
-20 |
|
|
|
673 – 1673 |
5 |
0.64-0.39 |
Material
|
e0(T) |
T range K |
Ref.
|
e range
|
||||
a |
b |
c |
d |
s.d. |
||||
Lightweight Refractories |
|
|
|
|
|
|
|
|
MPK 110 (20wt% Al2O3, 53wt% SiO2, 4wt% Fe2O3, 16wt% MgO) |
|
|
|
See Fig. 1
|
|
1073 – 1300 |
8.9 |
0.58-0.62 |
MPK 125 (36wt% Al2O3, 46wt% SiO2, 15wt% CaO) |
|
|
|
|
1063 – 1350 |
8.9 |
0.54-0.64 |
|
MPK 140 (41wt% Al2O3, 54wt% SiO2) |
|
|
|
|
1073 – 1350 |
8,9 |
0.48-0.55 |
|
MPK 155HA (61wt% Al2O3, 36wt% SiO2) |
|
|
|
|
1063 – 1350 |
8.9 |
0.44-0.36 |
|
MPK 130HSR (36wt% Al2O3, 54wt% SiO2) |
|
|
|
|
1073 – 1250 |
8.9 |
0.06-0.62 |
|
MPK SUPRA (11wt% Al2O3, 75wt% SiO2, 6wt% Fe2O3) |
|
|
|
|
1073 – 1300 |
8.9 |
0.64-0.81 |
|
Refractory Brick |
|
|
|
|
|
|
|
|
45wt% Al2O3, 55% SiO2; density = 330 kg/m3 |
|
|
|
|
|
See Fig. 1 |
10 |
See Fig. 1 |
45wt% Al2O3, 55% SiO2; density = 260 kg/m3 |
|
|
|
|
|
10 |
||
50wt% Al2O3, 50% SiO2; density = 240 kg/m3 |
|
|
|
|
|
10 |
||
50wt% Al2O3, 50% SiO2; density = 210 kg/m3 |
|
|
|
|
|
10 |
||
70wt% Al2O3, 26% SiO2; density = 200 kg/m3 |
|
|
|
|
|
10 |
||
45wt% Al2O3, 53% SiO2; density = 130 kg/m3 |
|
|
|
|
|
10 |
||
45wt% Al2O3, 55% SiO2; density = 100 kg/m3 |
|
|
|
|
|
10 |
||
100% SiO2; density = 100 kg/m3 |
|
|
|
|
|
10 |
||
100% SiO2; density = 80 kg/m3 |
|
|
|
|
|
10 |
Material |
e0(T) |
T range K |
Ref. |
e range |
||||
a |
b |
c |
d |
s.d. |
||||
Furnace refractory (80-90% Al2O3, 5-9%, SiO2) porous 1.2 pores/mm |
1.17 |
-50.6 |
|
|
|
673 – 1023 |
11 |
0.8-0.65 |
0.8 pores/mm |
1.13 |
-37.6 |
|
|
|
673 – 1023 |
11 |
0.88-0.74 |
0.4 pores/mm |
1.09 |
-29.8 |
|
|
|
673 – 1023 |
11 |
0.6-0.82 |
Refractory Brick |
|
|
|
|
|
|
|
|
Silica (97wt% SiO2, 2.6wt% CaO) |
|
|
|
|
|
See Fig 1 |
12 |
See Fig 1 |
Silica brick, used (as above) |
|
|
|
|
|
12 |
||
Zirconia silicate (32wt% SiO2, 63wt% ZrO) |
|
|
|
|
|
12 |
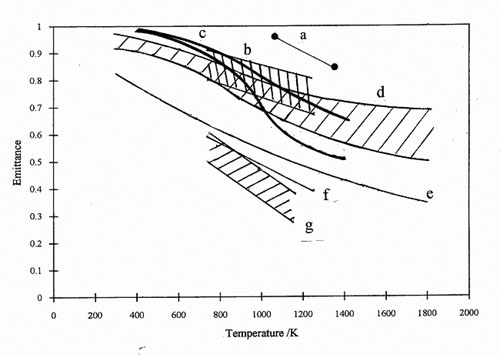
Fig. 1 Normal total emissivity of refractory materials based on aluminium and silicon oxides:
(a) carborundum-based high emissivity coating (8,9);
(b) permeable ceramic materials (10);
(c) ceramic fibres (normal, 6 and parallel, 6);
(d) silica bricks (14);
(e) Al2O3 mean line from Fig. 2;
(f) ceramic fibre board (11);
(g) light weight refractory (8,9).
Acknowledgements
This work was funded in part by the UK Heat Transfer and Fluid Flow Service (HTFS) and part supported by the UK EPSRC. The information contained within this file was first published in the Journal of the Institute of Energy. 74, No 500 September 2001 (pp 91 – 99). The permission of the UK Institute of Energy to reproduce it here is gratefully acknowledged.
Sources
1. TOULOUKIAN, Y.S. and DE WITT, D.P, Thermal radiative properties: Metallic elements and alloys, 1970, Vol. 7. TOULOUKIAN, Y.S. and DE WITT, D.P. Thermal radiative properties. Nonmetallic solids, 1971, Vol. 8; in Thermophysical Properties of Matter, TPRC Data Series (edited by Touloukian, Y.S. and Ho, C.Y.) Plenum Press, New York.
2. Handbook of Chemistry and Physics (60th Edition), CRC Press, Boca Raton, Florida, 1981.
3. RATANAPUPECH, P. and BAUTISTA, R.G. Normal spectral emissivities of liquid iron, liquid nickel and liquid iron-nickel alloys. High Temperature Science, 1981, 14(4) 269-283.
4. WILLIAMS, A., HAMPARTSOUMIAN, E. and SIMMONS, B. Unpublished data.
5. OSBORN, P.D. Handbook of Energy Data and Calculations. Butterworth, London, 1985.
6. FLETCHER, J.D. and WILLIAMS, A. Emissivities of ceramic fibre linings for high-temperature furnaces. JInst.Energy, 377, 1984
7. ELLISTON, D.G. GRAY, W.A., HIBBERD, D.F., HO, T-Y. and WILLIAMS, A. The effect of surface emissivity on furnace performance. JInst.Energy, 1987, 155-167.
8. GRAY, W.A., HAMPARTSOUMIAN, E., TAYLOR, J.M. and WILLIAMS, A. The role of radiation in determining the performance of gas-fired furnaces. Proc. 1989 Int. Gas Res. Conf., Government Institutes USA Inc., 1989, Vol. III, 26-34.
9. HAMPARTSOUMIAN, E. Spectral emittance measurements of furnace wall materials and coatings. Ceramics in Energy Applications Conference, Sheffield, IOP Publishing Ltd., 1990, 149-157.
10. JACKSON, J.D., YEN, C-C. Measurements of total and spectral emissivities of some ceramic fibre insulation materials. Ceramics in Energy Application, The Institute of Energy, London, 1994,159.
11. JACKSON, J.D., AN, P. and PENA-MARCO, I. Measurements of the total and spectral emittance of permeable ceramic materials. Proc. 4th UK National Heat Transfer Conference, C510/132, I.Mech.E., 1995, 561-565.
12. HOOGENDOORN, C.J. and WIERINGA, J.A. The effect of refractory emission on the energy efficiency of high temperature gas fired furnaces. VDI Beridte, 1989, 765, 133-141.
13. FISHER, G. Ceramic coatings enhance performance engineering. Ceramic Bulletin, 1986, 65(283).