-
How do I characterise pulverised coal using an Isothermal Plug Flow Reactor-IPFR?
Date posted:
-
-
Post Author
dev@edge.studio
The concept of pulverised fuel characterisation is introduced in
1. Background
The IPFR is used to investigate combustion characteristics of pulverised [GLOSS]Coal[/GLOSS] and other solid fuels under a number of well-controlled specific environments.
The reactor enables the coal to be evaluated at a wide variety of residence times under variable particle heating rates and combustion atmospheres. This flexibility enables the combustion performance of the coal to be studied under client/applications specified atmospheric conditions.
It is routinely used to investigate the following:
- Devolatilisation characteristics of solid fuels and their blends,
- Burnout and combustion rates of various chars,
- Ignition properties of solid fuels and blends,
- Nitrogen chemistry – fate of fuel nitrogen.
The reactor can be used to represent conditions found in full-scale combustion processes with heating rates in the order 104-105 K/s .
Fuel is injected into a well-defined combustion environment and collected after a residence time in the reactor between 5 to 1500 ms.
The Fuel conversion can be described with reaction kinetics on the basis of measurements made under these conditions. The application of kinetic data allows the prediction of the fuel behaviour under industrial conditions by means of mathematical modelling. The fuel characteristics can also provide a measure of the combustion performance relative to a reference fuel.
2. IPFR design
The Isothermal Plug Flow Reactor is constructed in three main sections – see Figure 1:
Gas Preheat section: This section contains the comburent generator fired with a 30kW natural gas burner. This pre-combustor provides hot flue gases in the range of 800º-1500ºC, which ensures that at the entrance of the reactor tube, high heating rates can be obtained. The pre-combustor product can also be mixed with an additional gas (e.g. CO2, CO, NOx, SOx, etc.) to change the composition of the inlet gases entering the reactor tube.
Reactor: The reactor tube consists of eight segments, which can be independently heated with SiC elements. In this way it is possible to adjust isothermal conditions within 10ºC over the whole reactor length. The tube has an operating length of 4 meters and an internal diameter of 150 mm. For pulverised fuel, a screw feeder system is used to supply a constant mass flow rate into the reactor.
Collection system: A sampling probe can be inserted in the base of the reactor to measure properties of solid particles at residence times in the range of 5 to 1500 ms. The particles are immediately quenched to temperatures below 200ºC to allow no further reaction. This allows the observation of processes such as particle heating, devolatisation, gasification, combustion (oxidation), reduction and defragmentation of solids.
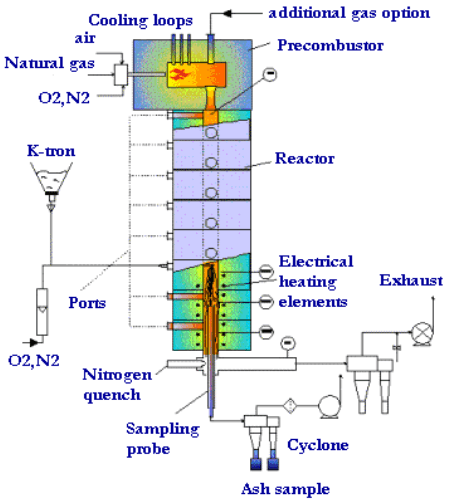
Figure 1: Diagram of the IPFR
The key features of the facility are given in the table below:
Reactor tube length | 4 m |
Reactor tube diameter | 150 mm |
Maximum thermal input | 60 kWNG+54kWe |
Maximum operating temperature | 1500 C |
Residence time range | 5 – 1500 ms |
Maximum flow rate | 75 Nm3/h |
Feeding rate of pulverised fuel | 0.05 -5 kg/h |
3. Coal Characterisation using the IPFR
3.1 Devolatilisation analysis
The High Temperature Volatile Matter (HTVM) released is determined by measurements in the Isothermal Plug Flow Reactor (IPFR). The importance of this measurement is described in CF183.
The standard measurement conditions for a pulverised fuel are typically 1200°C and 0% oxygen. Under these conditions the char is sampled at different residence times yielding a time dependent volatile release. An ash balance is applied for the difference in ash content of coal and char. The resulting mass loss corresponds to the released volatile matter.
A volatilisation curve is generally developed to have a graphic view of the data previously obtained. It serves to determine the rate of volatile release and the high temperature volatile matter yield both being important for flame stabilization, ignition and NOX emissions.
3.2 Char burnout analysis – see CF184
Char burnout analysis is made to determine kinetic data for char combustion rates as well as burnout times needed for complete combustion. Both are needed to predict the combustion performance of a boiler when an “unknown” fuel or a blend is fired.
The char burnout measurements are normally done at three different temperatures 950, 1200 and 1400°C at 4% oxygen and for the lowest temperature additionally at 8 and 12 % oxygen. Carbon content in ash (dry) is analysed at different residence times. With these data a char burnout curve can be set and the kinetic data can be studied.
3.3 Ignition properties analysis
Establishing the Characteristic Ignition Length ([GLOSS]CIL[/GLOSS]) is a way of expressing ignition characteristics of pulverised fuels. The IPFR is used to provide the required conditions to carry out the process.
The reactor wall temperatures are set to 1200°C by control of the electrical heating elements. Pre-combustor inputs are set to maintain a gas temperature of 1200°C, an oxygen concentration of 4% and a reactor velocity of 4m/s. The pulverised fuel is fed by gravimetric control through a screw feed. Atmospheric pressure is maintained in the reactor.
Under these conditions a water-cooled endoscope is fitted with a Charge Coupled Device [GLOSS]CCD Camera[/GLOSS], both inserted into an access port – see Figure 2.
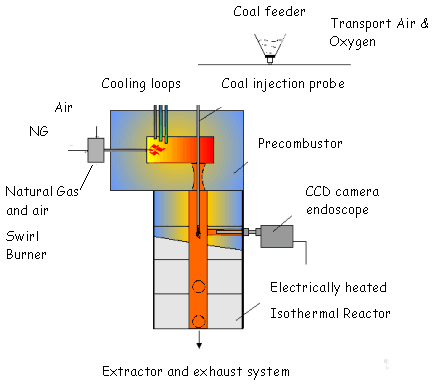
Figure 2: IPFR set-up for measurements of fuel ignition properties
Once the coal feed is initiated the approximate point of ignition can be brought into view by vertical adjustment of the injection probe. The observed ignition is then recorded on to videotape. This moving picture is converted to separate images and saved in hard copy. Time averaged representations are calculated by using the SCION image and SCIL software. From 100 images, a time-averaged image is used to define the Characteristic Ignition Length for the different coals. Figures 3 and 4 show the instantaneous image and the time-averaged analysis (100 frames) for a coal at feed rate of 1.5 kg/hr.
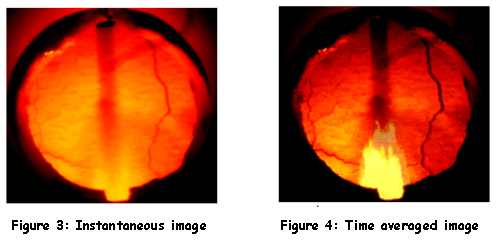
4. Conclusions
This combustion file outlines the use of an Isothermal Plug Flow Reactor to determine combustion characteristics of pulverised coal. The technique can be used also to determine the effect of coal blend changes on pf combustion performance. At the present time, the facility is being extended for the study the combustion characteristics of BioFuels and BioFuel/pulverised coal blends.
Sources
[1] Engineering Services: Coal characterisation for burner designers, boiler manufactures, and for mathematical modelling. IJmuiden, The Netherlands. IFRF Doc No C 76/y/7/6
[2] G. Gallagher, J. Haas, Reference report: Characterisation of weight loss and char burnout behaviour for El Cerejon Coal, IJmuiden, The Netherlands, 1996. IFRF Doc No 960927.
Acknowledgements
The author would like to acknowledge the work of a long list of IFRF investigators who have worked to develop this reactor during the last fifteen years.